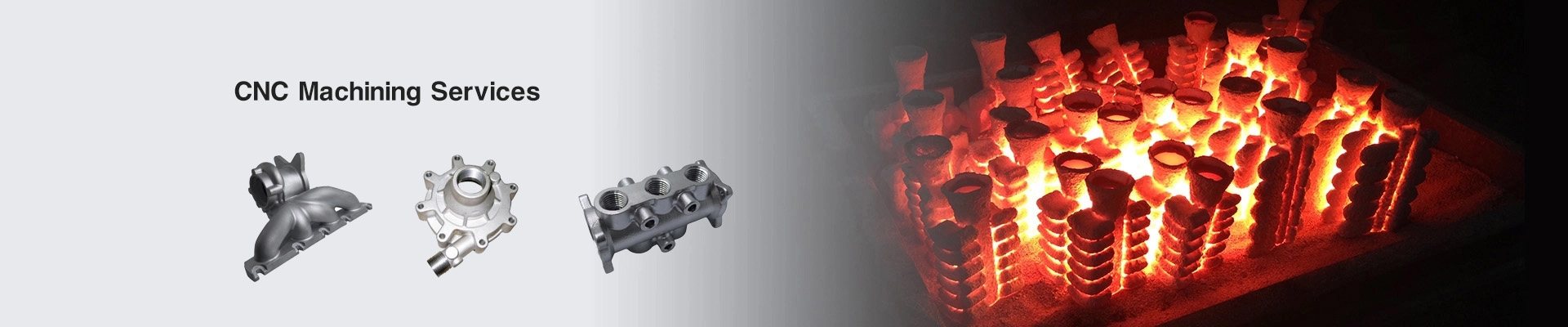
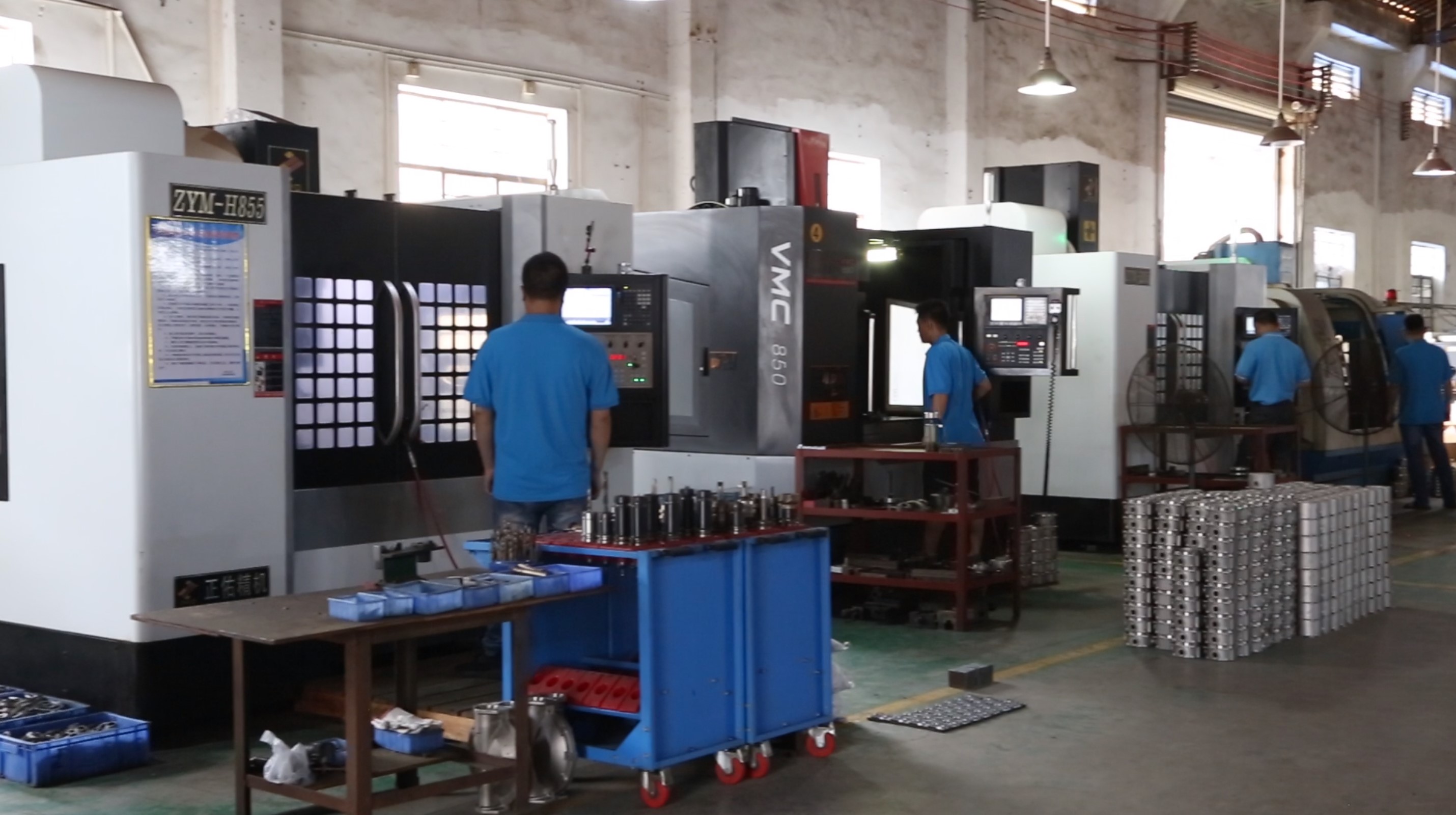
Feature | CNC Turning | CNC Machining | Wire Cutting | Manual Milling | EDM |
Best for | Cylindrical, conical, and round components | Complex geometries, multi-axis cuts,and detailed parts | Intricate contour cutting with high precision | Basic shaping, drilling, and surfacing | Creating highly complex shapes in hard metals |
Surface Finish | Smooth, high-quality finish | Requires post-processing for high-quality finishes | Requires polishing after cutting | Rougher surface finish compared to CNC machining | Produces extremely fine and detailed surface finishes |
Precision & Tolerances | High (±0.005mm) | Very high (±0.002mm) | Extremely high (±0.001mm) | Medium (±0.05mm) | Ultra-high precision (±0.0005mm) |
Complexity Handling | Good for rotational symmetry | Excellent for complex, multi-axis machining | Excellent for intricate patterns and fine cuts | Suitable for basic shapes but limited in complexity | Best for extremely intricate details and micro-machining |
Speed & Efficiency | Fast for cylindrical parts | Medium to fast for complex parts | Slow due to wire erosion process | Medium, depends on operator skill | Slowest among the five due to spark erosion |
Cost-Effectiveness | High for cylindrical parts | High for complex and batch production | High for precision cuts, but expensive for large parts | Low cost but requires more labor | Expensive due to electrode wear and slow processing speed |
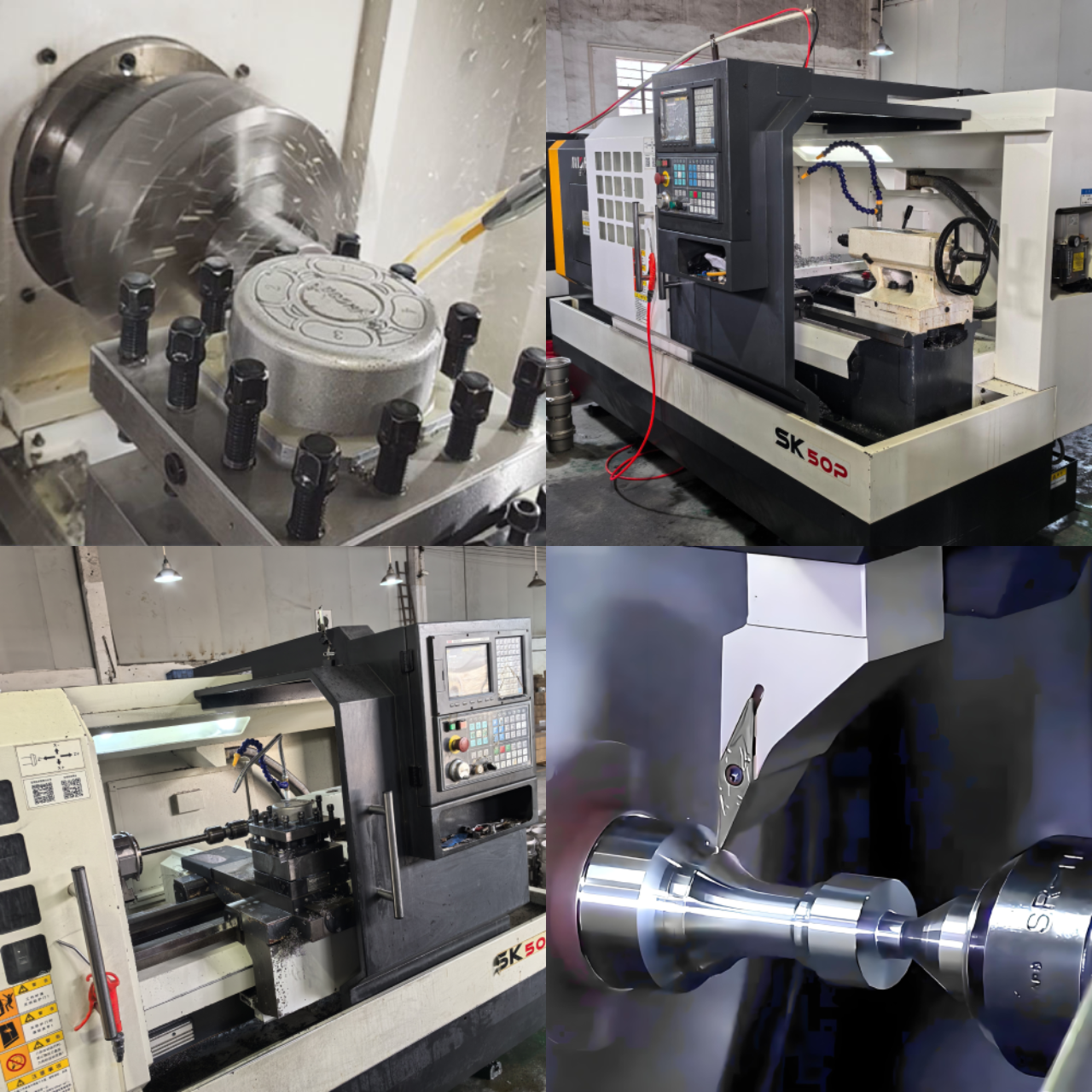
CNC Turning
CNC Turning is a high-precision machining process used to create cylindrical, conical, and complex rotational parts by removing material from a workpiece using a rotating cutting tool.
CNC Turning at Foshan Zeren ensures high-precision manufacturing of cylindrical and complex rotational parts for industries like automotive, aerospace, and marine. Using advanced multi-axis CNC lathes, we provide customized solutions with tight tolerances, superior finishes, and post-turning services such as heat treatment and coating, guaranteeing top-quality investment casting and machining results.
Working Principle:
1. The workpiece is securely mounted on a rotating spindle.
2. A stationary cutting tool moves along programmed paths to remove excess material and shape the final component.
3. CNC systems precisely control the cutting speed, tool movement, and feed rate, ensuring consistent accuracy and repeatability.
Key Features And Advantages
High Precision & Tight Tolerances:
Ensures consistency across large production runs with micron-level accuracy.
Efficient for Mass Production:
Capable of handling high-speed operations, reducing production time while maintaining quality.
Smooth Surface Finish:
Produces refined surfaces, minimizing the need for additional finishing processes.
Versatility:
Can process various materials, including stainless steel, aluminum, brass, titanium, and plastic.
Cost-Effective for Cylindrical Parts:
Ideal for components like shafts, bushings, screws, nozzles, and precision connectors.
Repeatability:
Delivers uniform parts in large-scale manufacturing with minimal variation.
CNC Machining
CNC Machining is a high-precision, automated manufacturing process that uses computer-controlled tools to remove material from a workpiece, shaping it into a desired form.
At Foshan Zeren, CNC machining is a core service that enables efficient production of complex components with tight tolerances and excellent surface finishes, making it ideal for aerospace, automotive, marine, and industrial applications.
Working Principle:
CNC Machining operates by using pre-programmed computer software to control cutting tools, guiding them to shape the workpiece with precision. The process includes:
1. Design: Parts are designed using CAD software.
2. Conversion: Designs are converted into CNC machine instructions (G-code).
3. Machining: Automated cutting tools shape the workpiece.
4. Inspection: Final inspection and finishing ensure accuracy and quality.
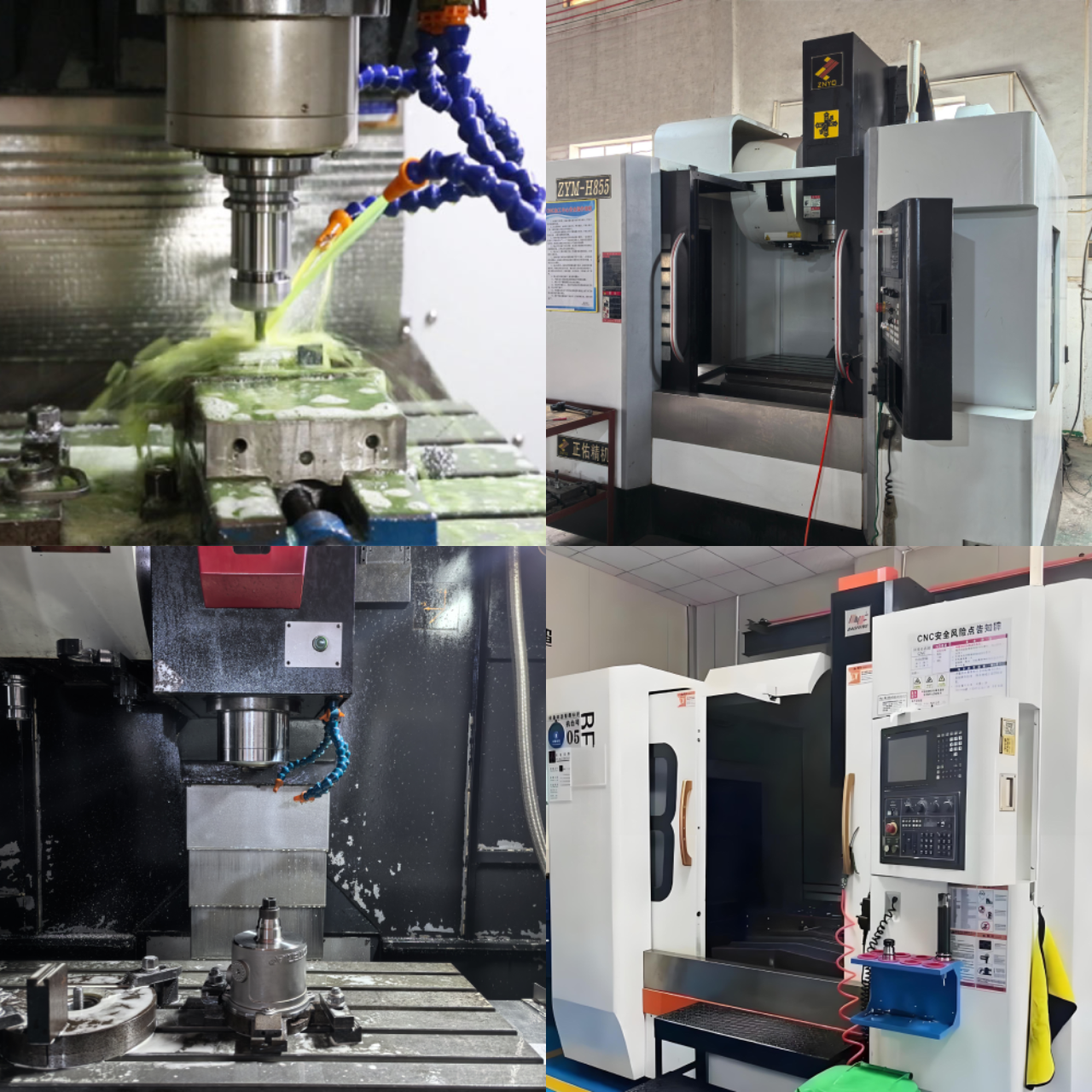
Key Features And Advantages
High Precision & Tight Tolerances:
Achieves accuracy levels of ±0.002mm, ensuring consistent quality.
Versatility:
Suitable for metals (steel, aluminum, titanium), plastics, and composites.
Multi-Axis Machining:
Supports 3-axis, 4-axis, and 5-axis machining, allowing complex part production.
Automation & Efficiency:
Reduces manual labor, improves speed, and minimizes errors.
Scalability:
Suitable for prototyping, small-batch, and mass production.
Excellent Surface Finish:
Produces smooth surfaces, reducing post-processing requirements.
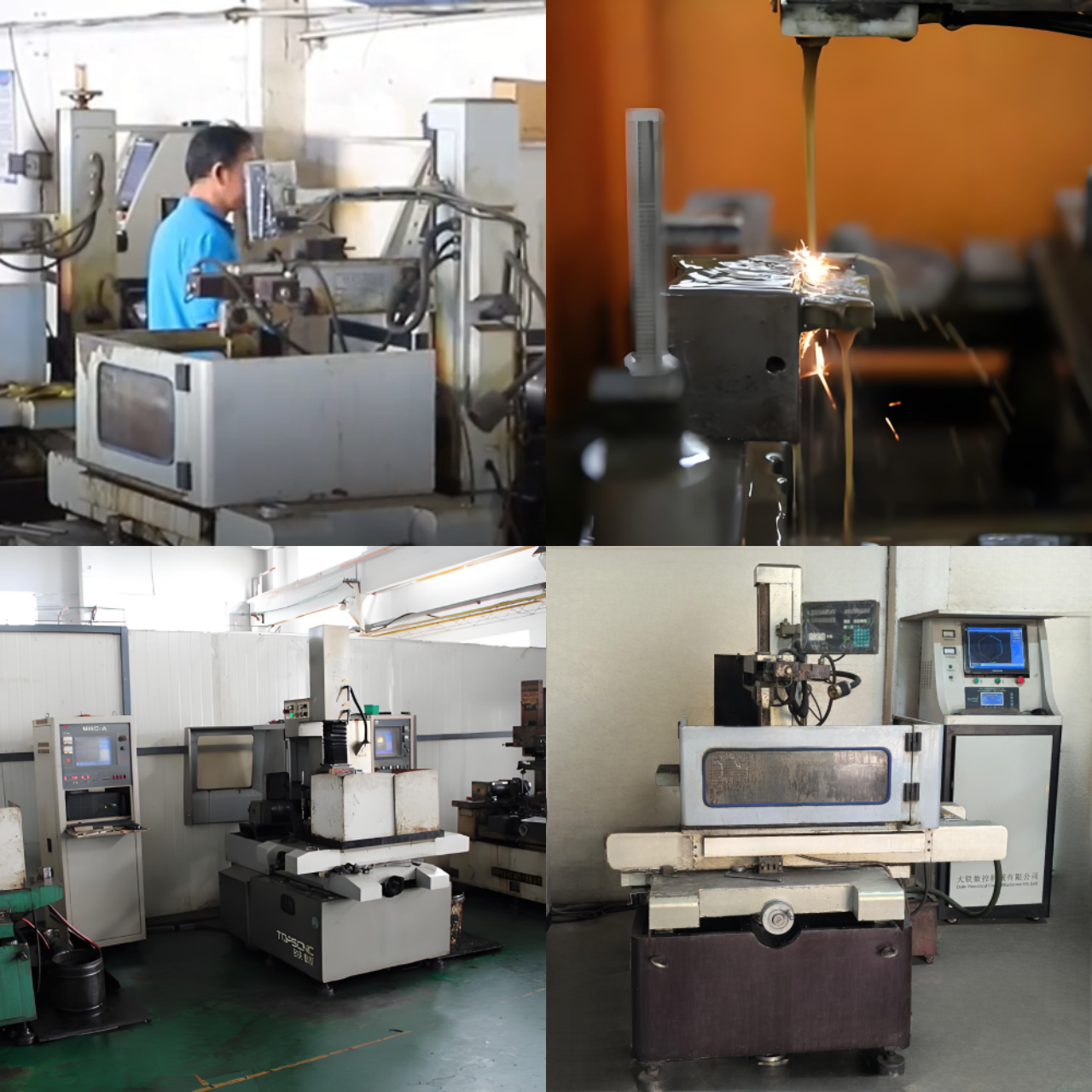
Wire Cutting
Wire Cutting is a high-precision, non-contact machining process that uses an electrically charged wire to cut conductive materials through electrical discharge erosion.
At Foshan Zeren, it is essential for manufacturing complex molds, aerospace components, and high-strength metal parts, ensuring tight tolerances, minimal material waste, and superior surface finishes.
Working Principle:
Wire EDM uses a thin, electrically charged wire to generate sparks, eroding the material without direct contact, for precise cutting.
The process includes:
1. Workpiece Immersion: The metal is placed in deionized water to cool and remove debris.
2. Wire Electrode Feeding: A thin wire moves along a programmed path.
3. Electrical Discharge: High-voltage sparks erode the material.
4. Precision Cutting: The wire cuts precise shapes with CNC programming.
5. Post-Cutting Processing: Polishing or finishing creates a smooth surface.
Key Features And Advantages
High Precision & Tight Tolerances:
Achieves ultra-high accuracy (±0.001mm), making it ideal for micro-machining.
Non-Contact Cutting:
No mechanical force applied, preventing tool wear and deformation.
Multi-Axis Machining:
Cuts intricate profiles, fine details, and internal geometries that traditional machining cannot achieve.
Minimal Material Waste:
Produces little to no material loss, maximizing efficiency.
Smooth Surface Finish:
Reduces the need for secondary finishing due to the fine cut quality.
No Need for Clamping Pressure:
Reduces workpiece stress and distortion, ensuring dimensional accuracy.
Manual Milling Machines
Manual milling machines are traditional machining tools that remove material from a workpiece using rotating cutting tools.
At Foshan Zeren, manual milling remains vital for prototyping, small-scale production, and custom modifications. It uses rotating cutting tools with operator-controlled feed rates, tool movements, and cutting depths, ensuring cost-effective, flexible, and precise machining for specialized applications.
Working Principle:
Manual milling machines shape parts by manually controlling the workpiece and cutting tool, adjusting spindle speed, cutting depth, and table movement.
Manual milling involves clamping the workpiece to a table, with the operator manually controlling the cutting tool's movement. Adjustments are made to spindle speed, cutting depth, and table movement for shaping.
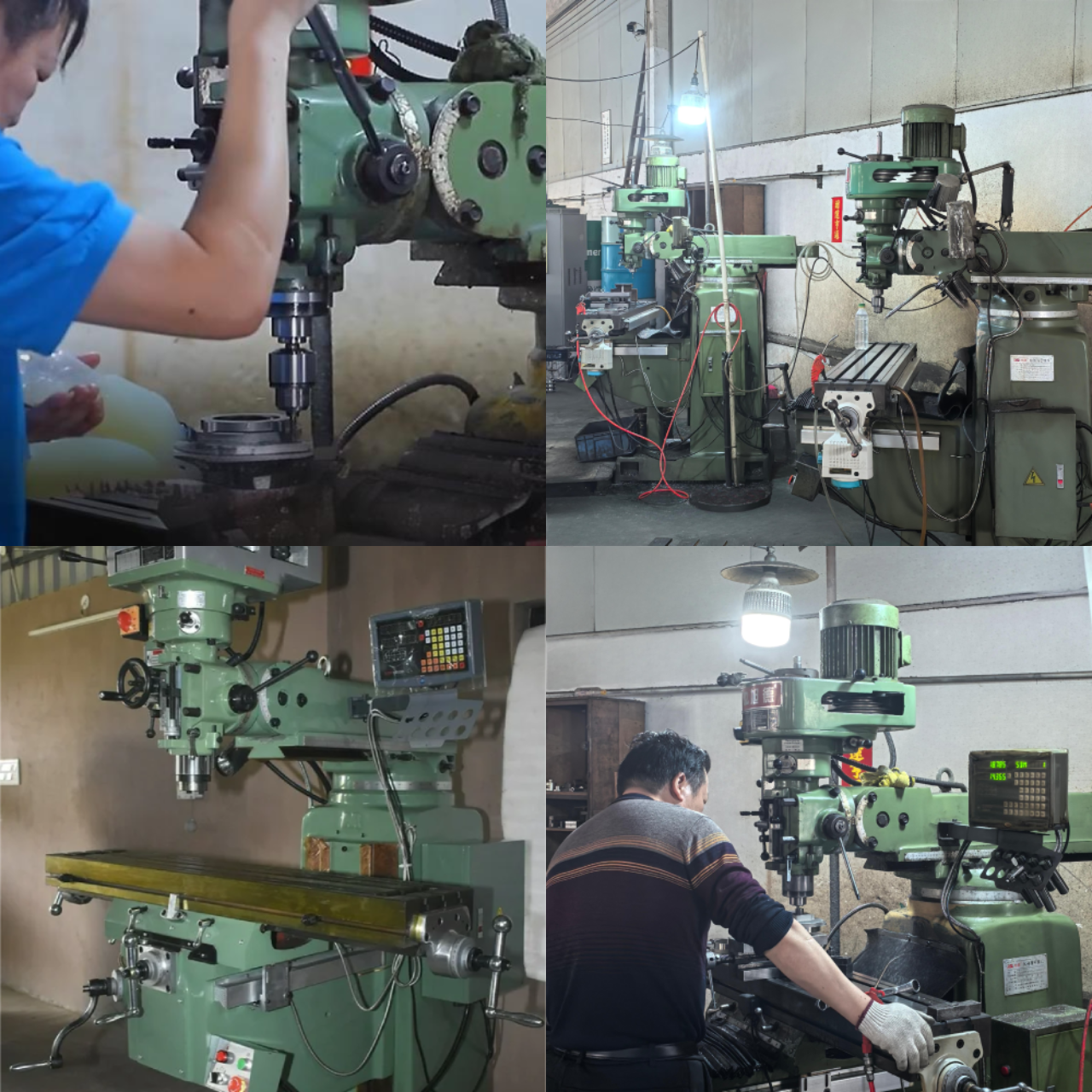
Key Features And Advantages
Operator Flexibility:
Allows skilled machinists to make real-time adjustments.
No Need for Programming:
Eliminates the need for CAD/CAM programming, saving time.
Hands-On Precision:
Useful for fine-tuning and custom machining.
Simple Setup & Maintenance:
Easier to operate and maintain compared to CNC machines.
Suitable for Small Batches:
Ideal for low-volume production, prototyping, and modifications.
Flexibility in Prototyping:
Ideal for one-off parts and modifications
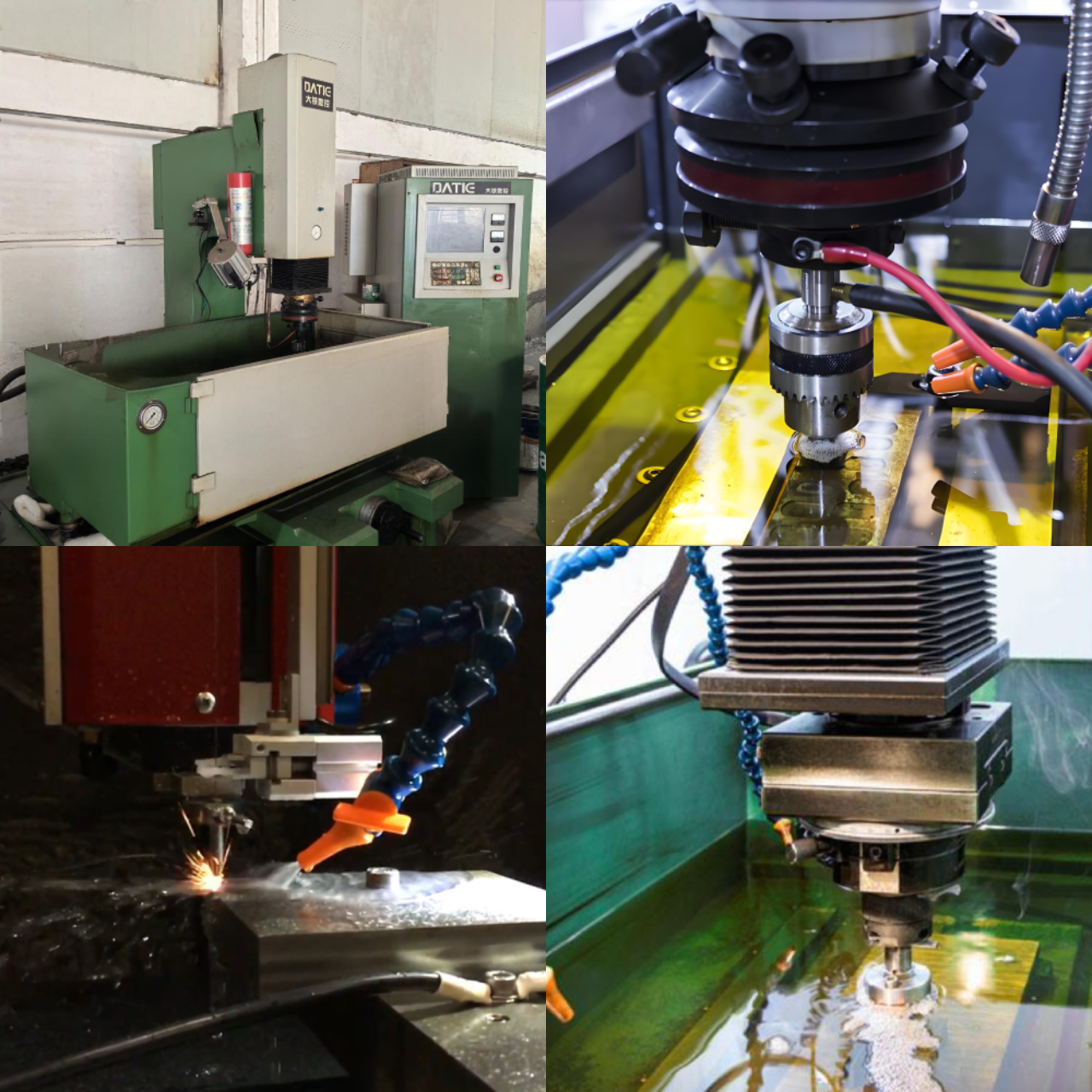
Electrical Discharge Machining (EDM)
EDM is a non-traditional, high-precision machining process that removes material from a workpiece through electrical discharges (sparks).
At Foshan Zeren, EDM precisely shapes hard metals using electrical discharges, ideal for intricate molds, aerospace components, and industrial parts requiring ultra-fine details, exceptional accuracy, and superior surface finishes.
Working Principle:
EDM uses electrical sparks to erode a conductive workpiece in dielectric fluid, shaping it precisely.
EDM Process:
1. Electrode Setup: Graphite or copper electrode positioned near the workpiece.
2. Dielectric Fluid Immersion: Workpiece submerged for cooling and debris removal.
3. Electrical Discharges: High-frequency sparks vaporize material.
4. Material Removal & Refinement: Debris flushed away for precision.
5. Final Finishing & Inspection: Polishing or heat treatment enhances properties.
Key Features And Advantages
Extreme Precision & Accuracy:
Achieves ultra-tight tolerances of ±0.0005mm, ideal for micro-machining.
No Mechanical Stress:
As a non-contact process, EDM prevents tool pressure, material distortion, and workpiece damage.
Works with Hard Materials:
Easily machines hardened steel, tungsten carbide, titanium, and superalloys.
Minimal Tool Wear:
Unlike traditional machining, EDM does not involve direct cutting, leading to longer tool life.
Capable of Micro-Machining:
Can create fine details and ultra-small features for electronics, medical, and aerospace components.
Complex Geometry Capability:
Can create intricate shapes, deep cavities, and sharp internal corners.
With advanced technology and years of expertise, Foshan Zeren Precision Casting Co., Ltd. delivers customized surface treatment solutions tailored to diverse industrial needs. Whether you require enhanced wear resistance, corrosion protection, or a refined finish, our precision-driven processes guarantee superior results. Trust us to provide cost-effective, durable, and aesthetically optimized metal finishing solutions for your business.
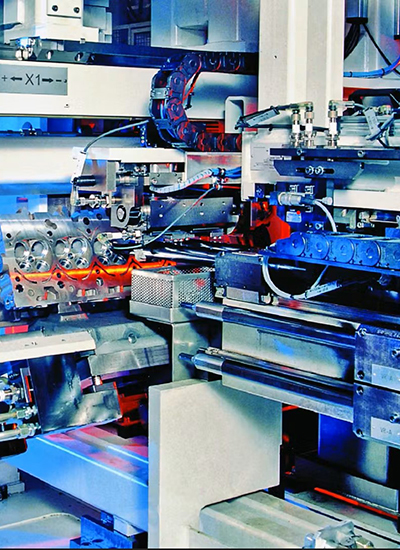
Agriculture
Machinery
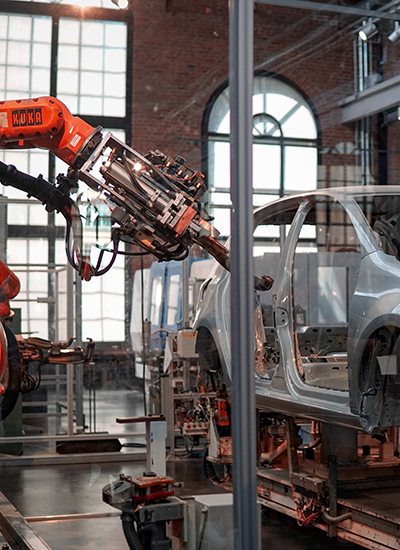
Automotive
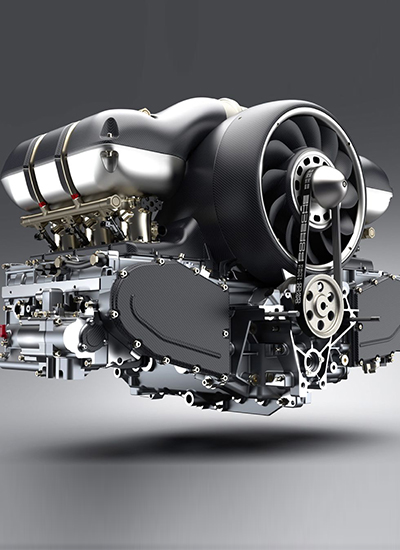
Energy
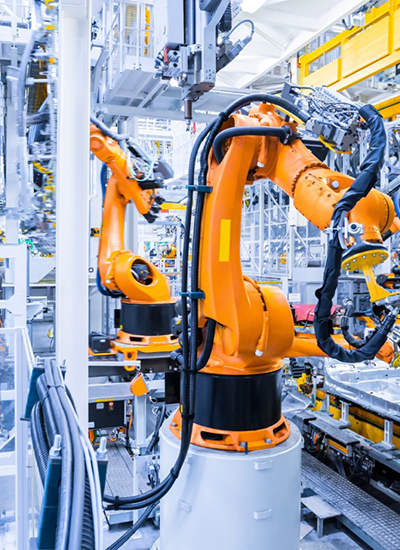
Industrial
Machinery
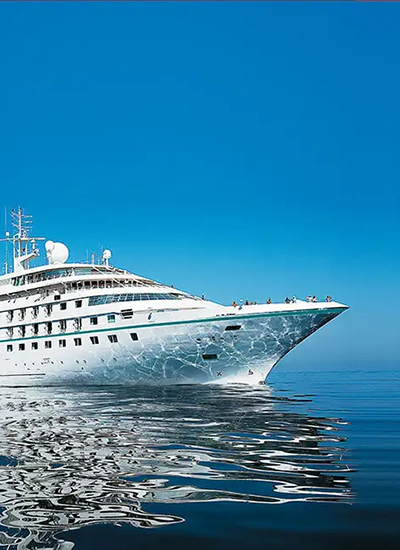
Marine
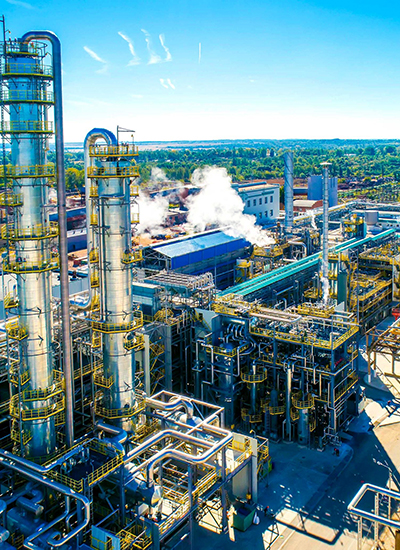
Petrochemical
Machinery
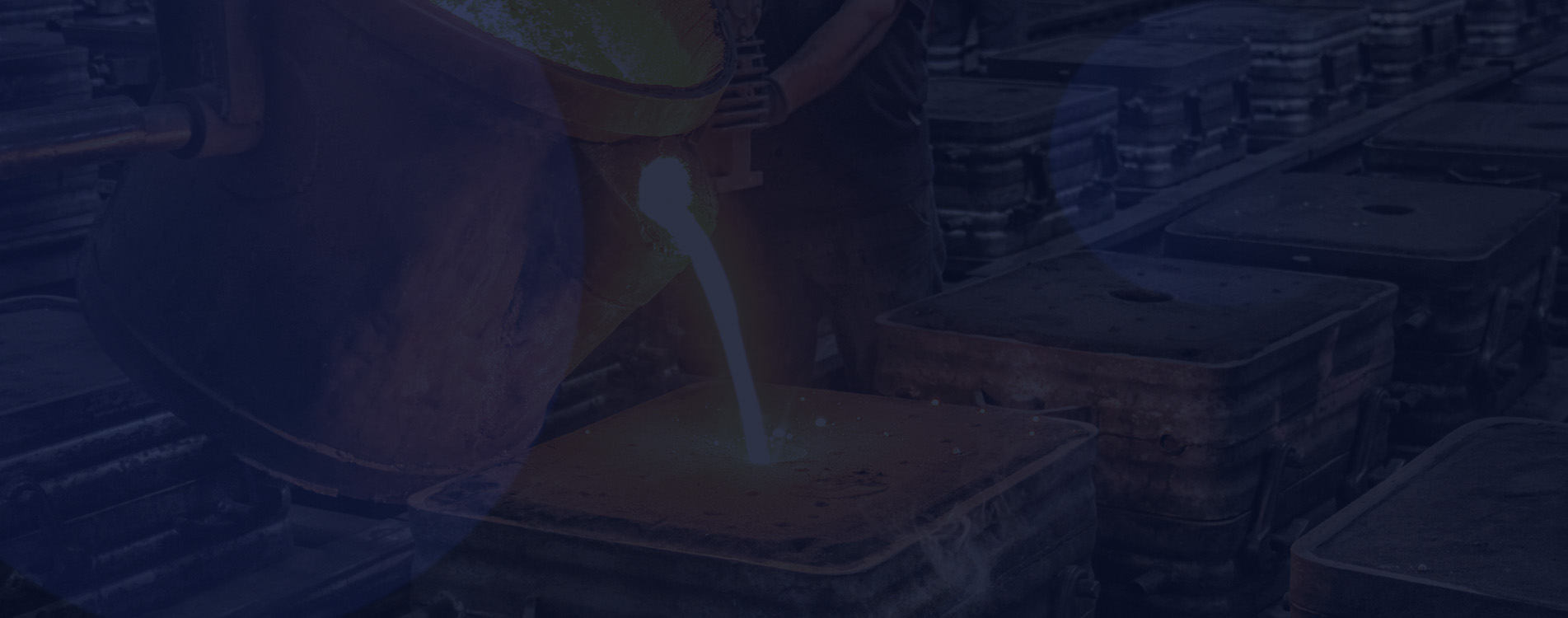
CONTACT US