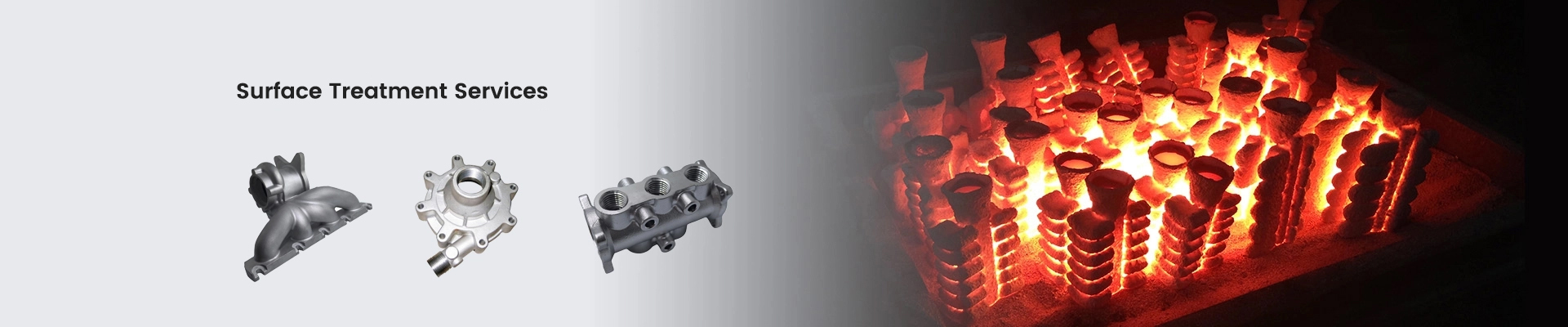
At Foshan Zeren Precision Casting Coompany, we specialize in high-quality surface treatment services to enhance the durability, corrosion resistance, and aesthetic appeal of metal components. Our expertise includes blackening, electroplating, electrophoresis, polishing, mechanical polishing, electrolytic polishing, and powder coating, ensuring that every product meets the highest industry standards for performance and longevity.
Comparison Table of Heat Treatment Processes
Process | Durability | Corrosion Resistance | Aesthetic Appeal | Cost | Maintenance Needs |
Blackening (Oxidation) | Medium | Moderate (needs oiling) | Matte black | Low | Requires oiling to prevent rust |
Electroplating | High | High | Shiny or matte | Medium | Minimal, but may tarnish over time |
Electrophoresis (E-Coating) | High | High | Uniform finish | Medium | Low maintenance |
Polishing | Low | None | High gloss | Low | Requires frequent cleaning |
Mechanical Polishing | Medium | None | Smooth surface | Medium | Requires surface protection |
Electrolytic Polishing | High | High | Ultra-smooth, reflective | High | Low maintenance |
Powder Coating | Very High | Very High | Various colors, matte/glossy | Medium-High | Very low maintenance |
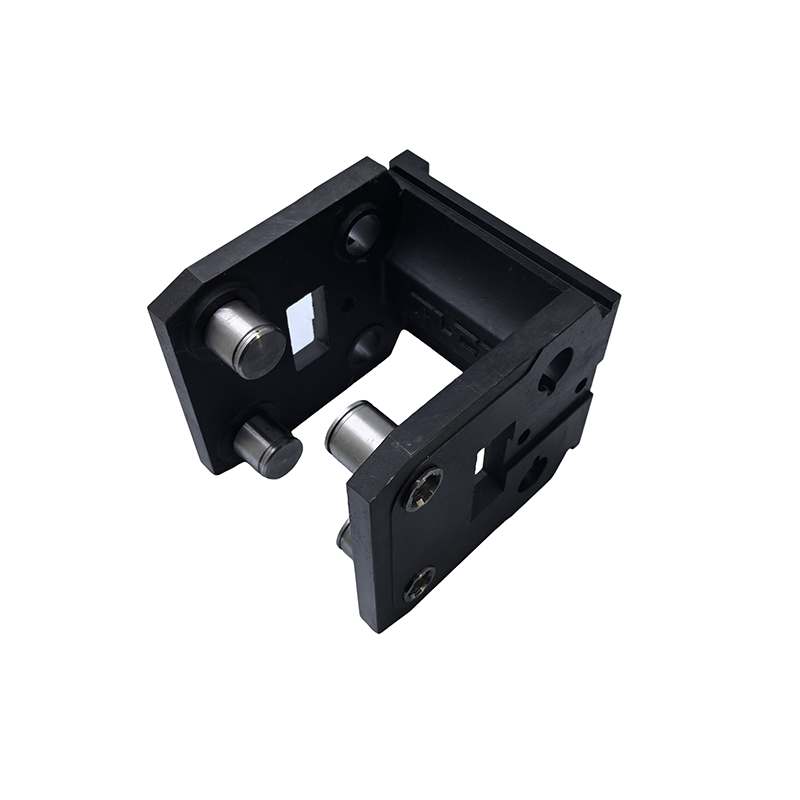
Blackening (Oxidation)
Blackening, also known as black oxide treatment, is a chemical conversion coating that creates a thin black oxide layer on metal surfaces. This process enhances corrosion resistance and improves the aesthetic appeal of metal components while maintaining dimensional accuracy, as the coating thickness is minimal.
>>>> Performance & Functional Benefits of Blackening
Corrosion Resistance
Forms a protective black oxide layer that helps reduce oxidation and rust, especially when sealed with oil or wax.
Minimal Dimensional Change
The oxide layer is extremely thin (typically 0.5-2 μm), preserving the original dimensions and precision of the part.
Reduced Light Reflection
Produces a matte black, non-reflective surface, making it ideal for military, firearm, and industrial applications where glare reduction is important.
Improved Wear Resistance
The blackened surface reduces friction, enhancing performance in moving or high-contact parts like tools, fasteners, and gears.
>>>> Cost-Effectiveness & Production Efficiency of Blackening
Lower Cost Compared to Plating & Coating
Blackening is more affordable than electroplating, powder coating, or anodizing, making it an economical choice for bulk production.
Fast Processing Time
The black oxide treatment can be completed in minutes, making it highly suitable for large-scale manufacturing with tight deadlines.
>>>> Blackening (Oxidation) is Best for Clients Who
Need Cost-Effective Corrosion Protection
Ideal for industries requiring basic rust prevention at a low cost, especially for tools and machinery.
Require Precision Components
Suitable for tight-tolerance parts since the thin oxide layer does not alter dimensions.
Prefer a Matte, Non-Reflective Finish
Best for firearms, military equipment, and industrial tools to reduce glare and improve aesthetics.
Need Improved Wear & Friction Performance
Ideal for gears, fasteners, and mechanical components, reducing friction and enhancing durability.
Electroplating
Electroplating is a widely used surface treatment process that enhances the appearance, durability, and corrosion resistance of metal components by depositing a thin metal coating (such as zinc, nickel, chrome, or gold) through electrochemical deposition.
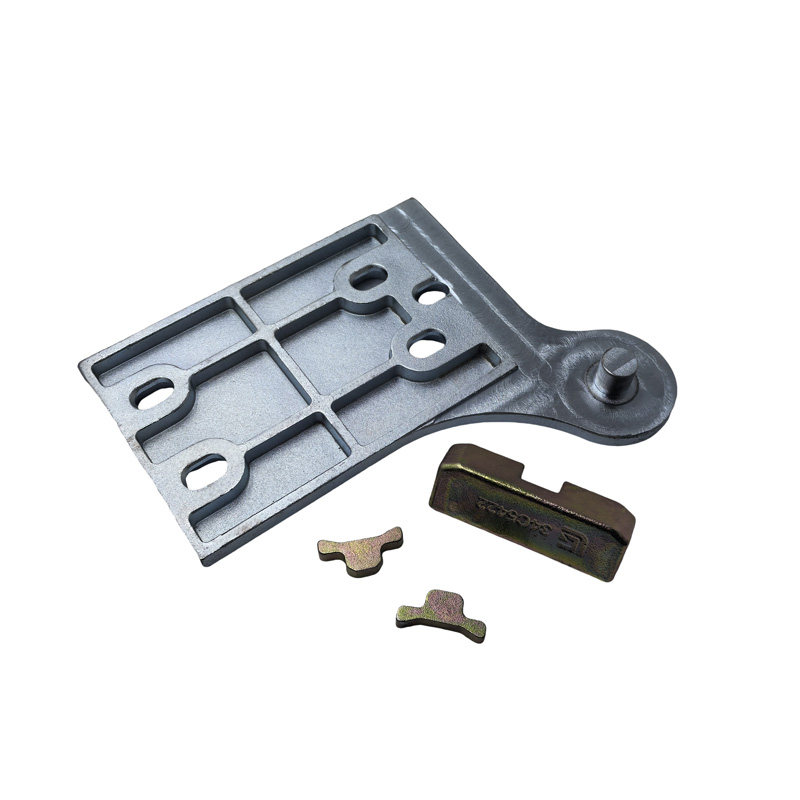
>>>> Performance & Functional Benefits of Electroplating
Enhanced Corrosion Resistance
Provides superior protection against rust and oxidation, especially for parts exposed to moisture and chemicals.
Increased Conductivity
Gold, silver, or copper plating can improve electrical conductivity, making it ideal for electronic components.
Aesthetic Appeal
Provides a shiny, decorative finish ideal for cosmetic applications, such as jewelry, automotive parts, and accessories.
Precision Coating
The process allows for thin, precise layers of metal to be applied, which can improve the functionality of components, especially in precision machinery.
>>>> Cost-Effectiveness & Production Efficiency of Electroplating
Affordable Process
Electroplating is a cost-effective solution, especially for improving the properties of inexpensive base metals.
Scalable
Ideal for both small batches and mass production, ensuring flexibility in meeting varying production needs.
>>>> Electroplating is Best for Clients Who
Need Superior Corrosion Resistance
Ideal for automotive, aerospace, and industrial components requiring long-term protection against rust and oxidation.
Require High-Quality Aesthetic Finishes
Perfect for luxury goods, jewelry, and decorative metal parts, offering shiny, matte, or textured finishes.
Seek Enhanced Electrical Conductivity
Best for electronics and electrical components, as plating with gold, silver, or copper improves conductivity and performance.
Need Wear & Abrasion Resistance
Suitable for machine parts, tools, and automotive components, where nickel or chrome plating provides hardness and durability.
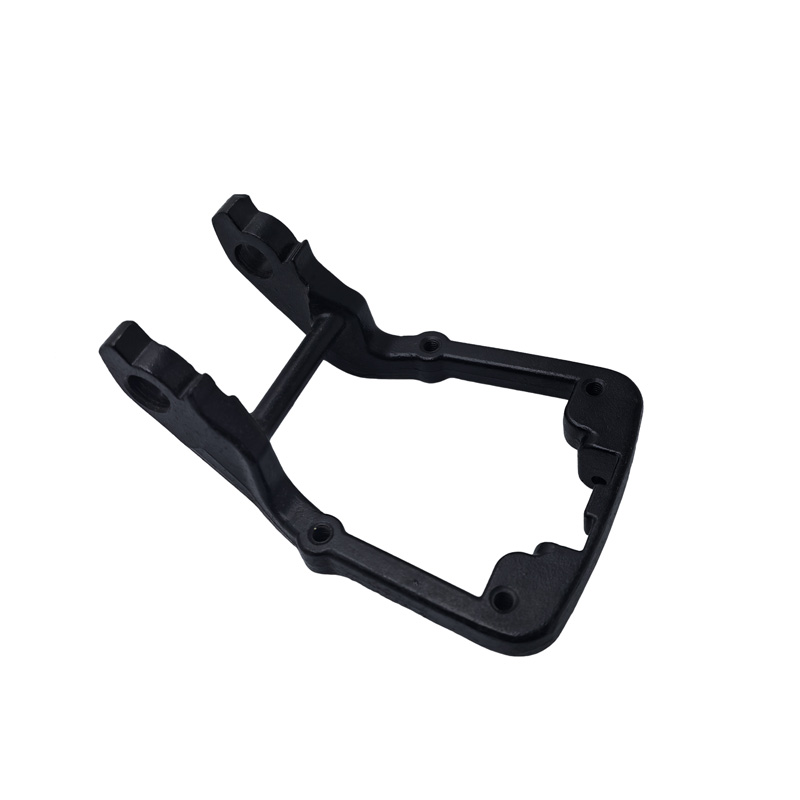
Electrophoresis (E-Coating)
Electrophoresis (E-Coating) is a high-performance, environmentally friendly surface treatment process that uses an electrical field to apply a polymer coating onto metal parts. It offers outstanding corrosion resistance, durability, and aesthetic appeal, making it ideal for automotive, industrial, and electronic components.
>>>> Performance & Functional Benefits of Electrophoresis
Superior Corrosion Resistance
Provides long-lasting protection against rust and oxidation, especially in harsh environments.
Uniform Coating
Ensures even coverage, including hard-to-reach areas like edges, corners, and holes.
Excellent Wear & Abrasion Resistance
Ideal for parts exposed to mechanical stress and friction, extending product lifespan.
Chemical Resistance
Protects parts from oils, solvents, and acids, enhancing their durability in challenging environments.
>>>> Cost-Effectiveness & Production Efficiency of Electrophoresis
Fast Processing Time
The automated process ensures quick application, suitable for large-volume production.
High Scalability
Ideal for mass production with minimal labor requirements.
>>>> Electrophoresis (E-Coating) is Best for Clients Who
Need Superior Corrosion Protection
Ideal for automotive, industrial, and electronic components, offering long-lasting rust and chemical resistance.
Require Uniform Coating on Complex Shapes
Perfect for intricate parts with edges, holes, and recesses, ensuring even coverage.
Seek an Eco-Friendly Coating Solution
Best for companies prioritizing low-VOC, water-based coatings that comply with environmental regulations.
Want a Cost-Effective, High-Volume Production Process
Suitable for mass production, as automated E-coating ensures efficiency, consistency, and minimal material waste.
Polishing
Polishing is a surface treatment process that improves the smoothness, appearance, and finish of a material by removing micro-level imperfections. It is commonly used for metal, plastic, and ceramic parts to achieve a glossy, reflective surface. Polishing enhances aesthetic appeal and functional performance, making it ideal for products in the automotive, electronics, and luxury goods industries.
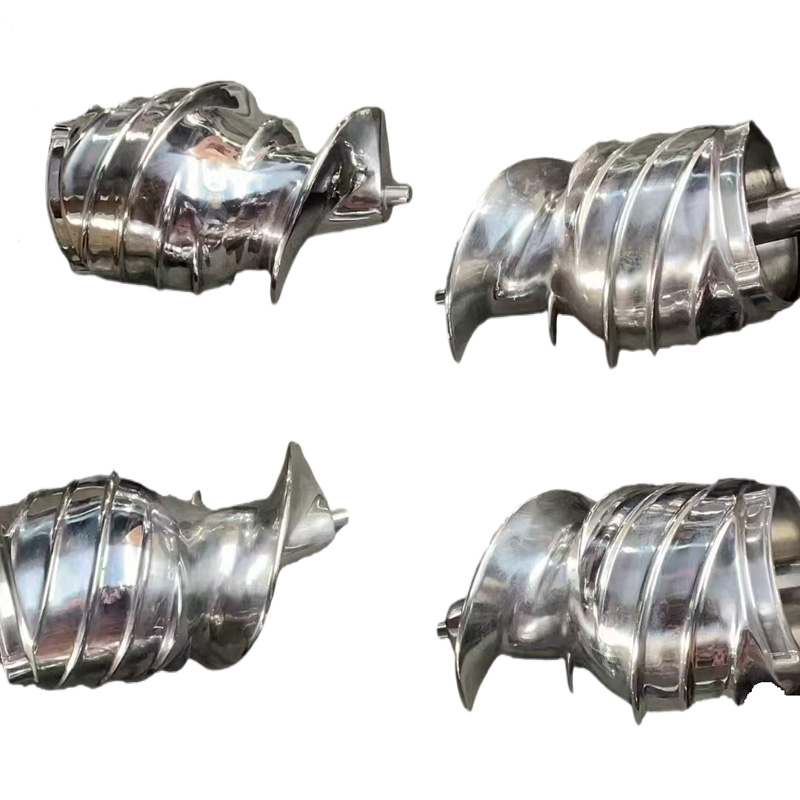
>>>> Performance & Functional Benefits of Polishing
Improved Aesthetic Appearance
Polishing enhances the shine and gloss of materials, providing a high-quality finish that elevates the overall look of products.
Enhanced Surface Smoothness
Removes microscopic scratches and imperfections, providing a smooth, reflective surface that is often desirable for decorative applications.
Reduced Friction
Polishing reduces surface roughness, leading to lower friction between moving parts, which can improve performance and lifespan in mechanical applications.
Corrosion Resistance
A polished surface can improve resistance to corrosion by reducing the accumulation of dirt and moisture, making it easier to clean and maintain.
>>>> Cost-Effectiveness & Production Efficiency of Polishing
Low-Cost Process
Polishing is a relatively low-cost process, especially compared to electroplating or other coating methods.
Quick Process
Polishing is a fast procedure that can be applied to a wide range of materials, ensuring efficient production.
>>>> Polishing is Best for Clients Who
Need a High-Gloss, Aesthetic Finish
Ideal for luxury goods, jewelry, automotive, and decorative metal parts requiring a shiny, mirror-like appearance.
Require Smooth, Low-Friction Surfaces
Best for precision components, medical devices, and mechanical parts where reduced surface roughness enhances performance.
Want to Improve Corrosion Resistance
Suitable for industries needing easy-to-clean, corrosion-resistant surfaces, such as food processing and medical applications.
Seek a Cost-Effective Surface Enhancement
A budget-friendly option for enhancing appearance and functionality without additional coatings or plating.
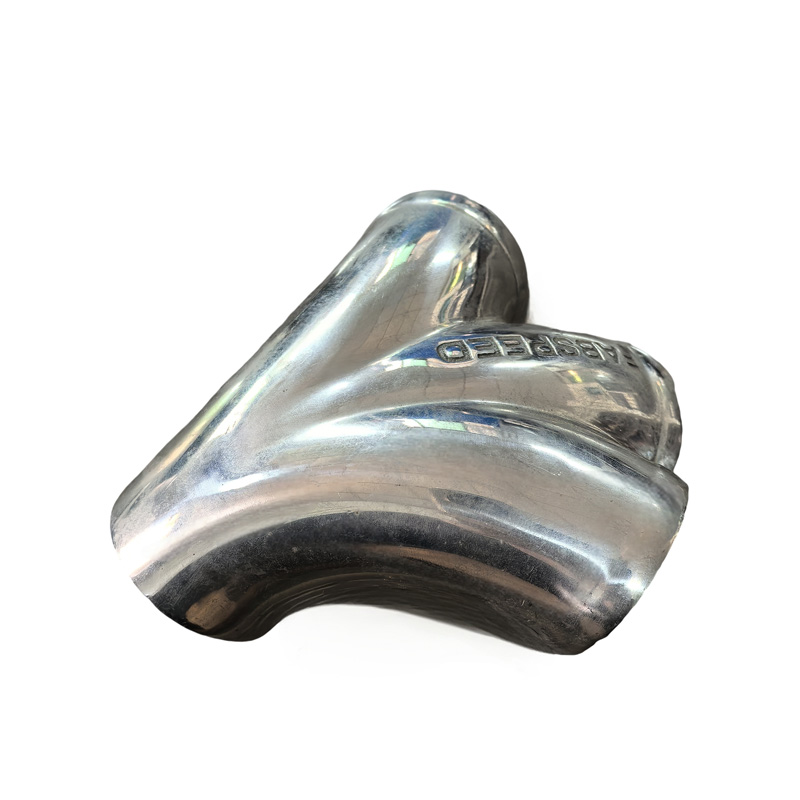
Mechanical Polishing
Mechanical polishing is a surface finishing process that uses abrasive tools to smooth and enhance the surface of materials like metal, plastic, and ceramics. It is often used to achieve a smooth, shiny finish, remove surface imperfections, and improve the aesthetic appeal and performance of components. Mechanical polishing is a commonly employed technique in the automotive, aerospace, and consumer goods industries.
>>>> Performance & Functional Benefits of Mechanical Polishing
Smooth Surface Finish
Mechanical polishing provides a high-quality, smooth surface, improving aesthetic appeal and reducing imperfections like scratches and blemishes.
Improved Friction
Polishing lowers surface roughness, reducing friction between components, which can improve performance and extend product life.
Enhanced Corrosion Resistance
By smoothing the surface, polishing can help prevent corrosion by reducing the adhesion of dirt and moisture.
Improved Light Reflectivity
The glossy finish achieved through mechanical polishing increases light reflectivity, ideal for decorative parts and luxury products.
>>>> Cost-Effectiveness & Production Efficiency of Mechanical Polishing
Relatively Low Cost
Mechanical polishing is an affordable process, especially for small to medium-scale production.
Efficient Process
The process is quick and effective at improving surface quality, making it suitable for both high-volume production and custom applications.
>>>> Mechanical Polishing is Best for Clients Who
Need a Smooth, High-Quality Surface Finish
Ideal for stainless steel, medical devices, and precision machinery requiring low surface roughness.
Require Friction Reduction for Moving Parts
Best for automotive, aerospace, and industrial components, where reduced friction enhances performance and longevity.
Want to Improve Corrosion Resistance
Suitable for food processing, pharmaceutical, and marine industries, as polishing removes surface contaminants and prevents oxidation.
Seek a Cost-Effective, Non-Coating Solution
Perfect for clients wanting aesthetic and functional surface improvement without adding extra coatings or chemicals.
Electrolytic Polishing
Electrolytic polishing is an advanced surface finishing process that uses electrochemical reactions to smooth and brighten metal surfaces. It effectively removes microscopic imperfections, improving both the aesthetic appearance and functional properties of metal parts. This technique is widely used in industries like automotive, medical, and aerospace, where precision, cleanliness, and corrosion resistance are critical.
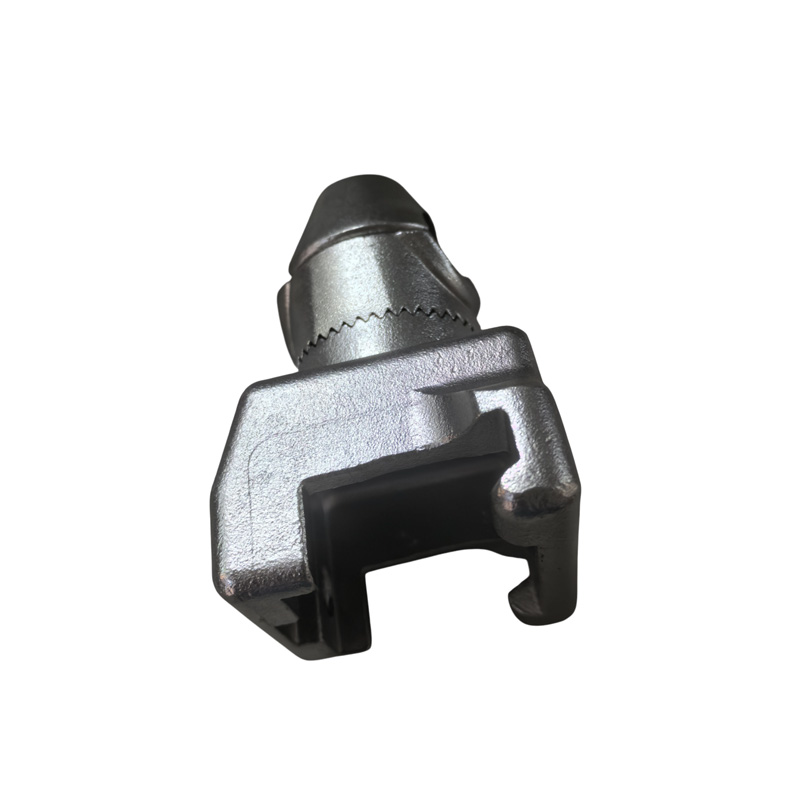
>>>> Performance & Functional Benefits of Electrolytic Polishing
Superior Surface Smoothness
Electrolytic polishing creates a mirror-like finish, improving the smoothness and appearance of parts.
Enhanced Corrosion Resistance
The process reduces surface roughness, creating a passivated layer that improves corrosion resistance, making parts more durable in harsh environments.
Improved Cleanliness
Ideal for applications in hygienic environments, electrolytic polishing helps achieve ultra-clean surfaces, essential for industries like medical and food processing.
Increased Durability
The smooth, passivated surface enhances the wear resistance and long-term durability of parts, especially in high-stress applications.
>>>> Cost-Effectiveness & Production Efficiency of Electrolytic Polishing
Efficient Process
Electrolytic polishing is a fast process that produces a high-quality finish with minimal material waste.
Energy-Efficient
Compared to traditional mechanical polishing, electrolytic polishing consumes less energy and reduces wear on tools.
>>>> Electrolytic Polishing is Best for Clients Who
Need Ultra-Smooth, High-Purity Surfaces
Ideal for medical devices, food processing equipment, and pharmaceutical components requiring a clean, contamination-free finish.
Require Enhanced Corrosion Resistance
Best for stainless steel and aerospace components, as the process removes surface imperfections and passivates the metal.
Want a Mirror-Like, Reflective Finish
Suitable for precision instruments, luxury goods, and high-end architectural elements demanding a shiny, polished appearance.
Seek a Low-Maintenance, Long-Lasting Surface
Perfect for industries needing durable, oxidation-resistant parts with minimal upkeep over time.
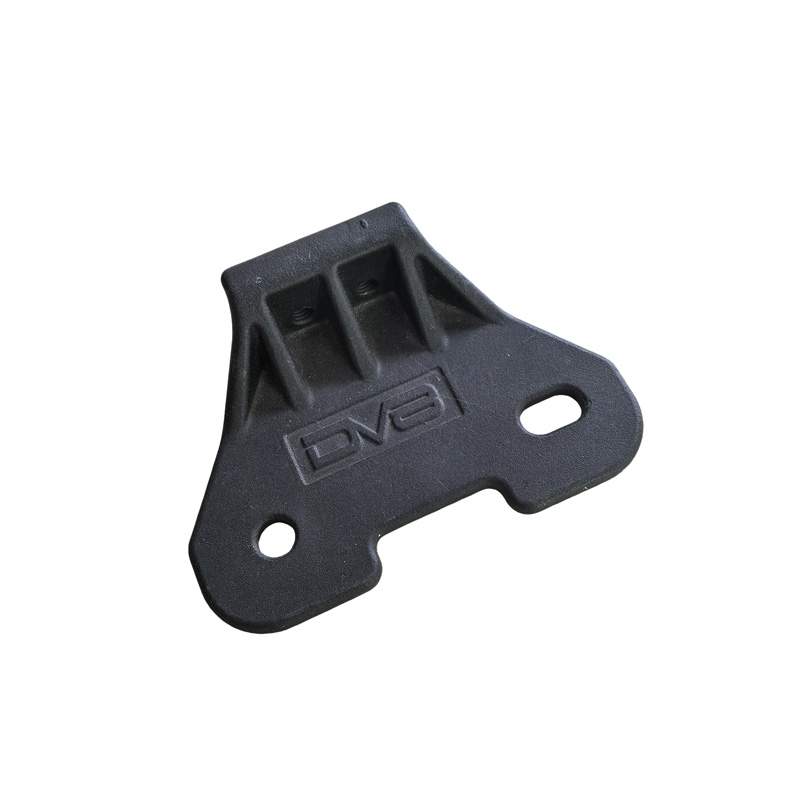
Powder Coating
Powder coating is a dry finishing process where a powdered coating is applied electrostatically to a metal surface and then cured under heat. It creates a durable, uniform finish that is resistant to abrasion, corrosion, and chemical exposure. Powder coating is ideal for metal parts in industries such as automotive, appliances, and furniture where durability and appearance are crucial.
>>>> Performance & Functional Benefits of Powder Coating
Durability
Powder coating provides a tough, long-lasting finish, significantly enhancing abrasion resistance and corrosion protection compared to conventional liquid coatings.
Even Coverage
It creates a uniform, smooth finish without the need for primers or solvents, ensuring better coverage and less waste.
Variety of Finishes
Available in various textures and colors, powder coating offers a wide range of decorative finishes for aesthetic applications.
Environmental Resistance
Powder-coated surfaces withstand UV light, extreme temperatures, and chemicals, making them ideal for outdoor applications.
>>>> Cost-Effectiveness & Production Efficiency of Powder Coating
Cost-Effective
Powder coating is cost-effective due to its low material waste, as excess powder can be reused.
Minimal Post-Treatment
The need for primers, solvents, or additional curing is eliminated, reducing overall production time and costs.
>>>> Powder Coating is Best for Clients Who
Need a tough, scratch-resistant finish
Ideal for automotive, industrial, and machinery parts.
Require strong corrosion and weather resistance
Perfect for outdoor furniture, construction, and marine equipment.
Want customizable colors and textures
Suitable for appliances, consumer goods, and decorative items.
Prefer an eco-friendly, cost-effective solution
Great for high-volume, solvent-free, and energy-efficient production.
With advanced technology and years of expertise, Foshan Zeren Precision Casting Co., Ltd. delivers customized surface treatment solutions tailored to diverse industrial needs. Whether you require enhanced wear resistance, corrosion protection, or a refined finish, our precision-driven processes guarantee superior results. Trust us to provide cost-effective, durable, and aesthetically optimized metal finishing solutions for your business.
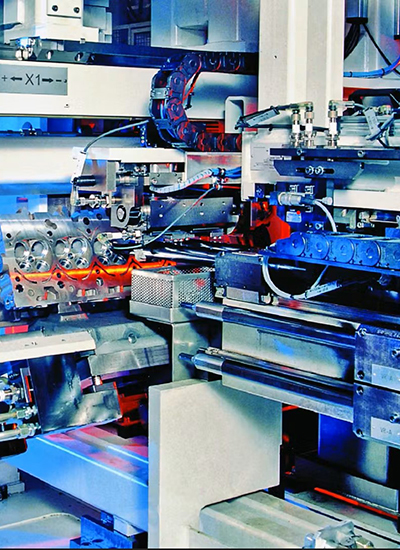
Agriculture
Machinery
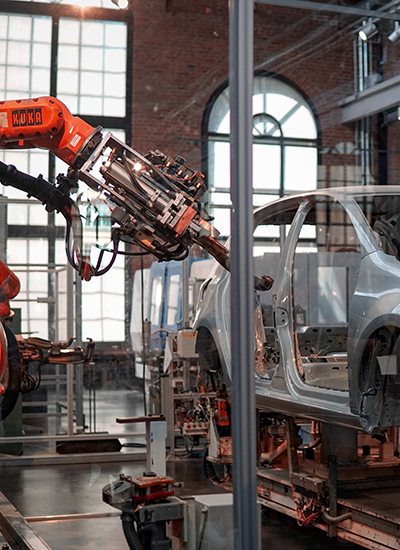
Automotive
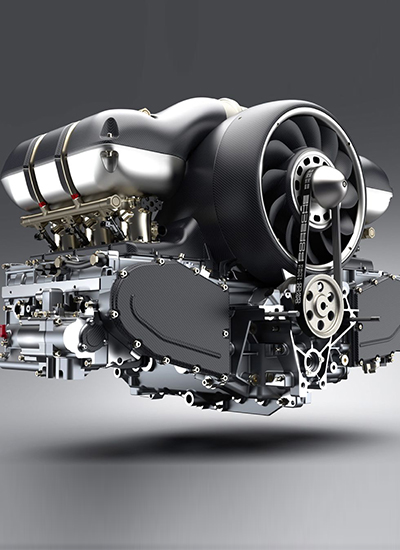
Energy
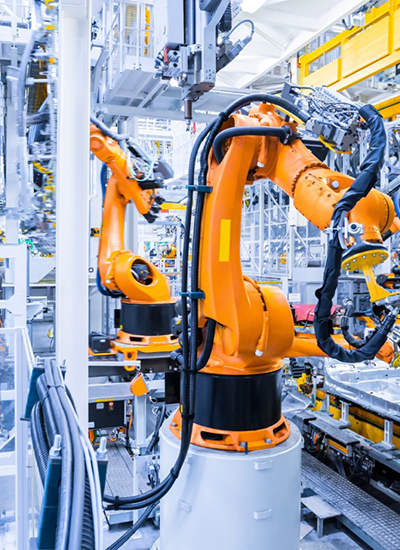
Industrial
Machinery
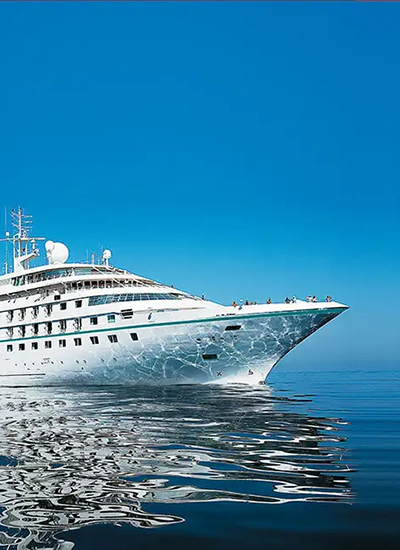
Marine
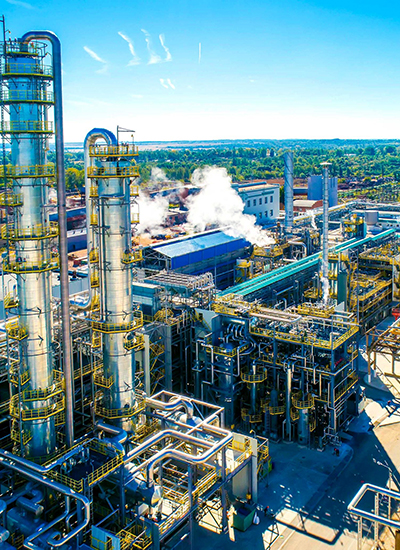
Petrochemical
Machinery
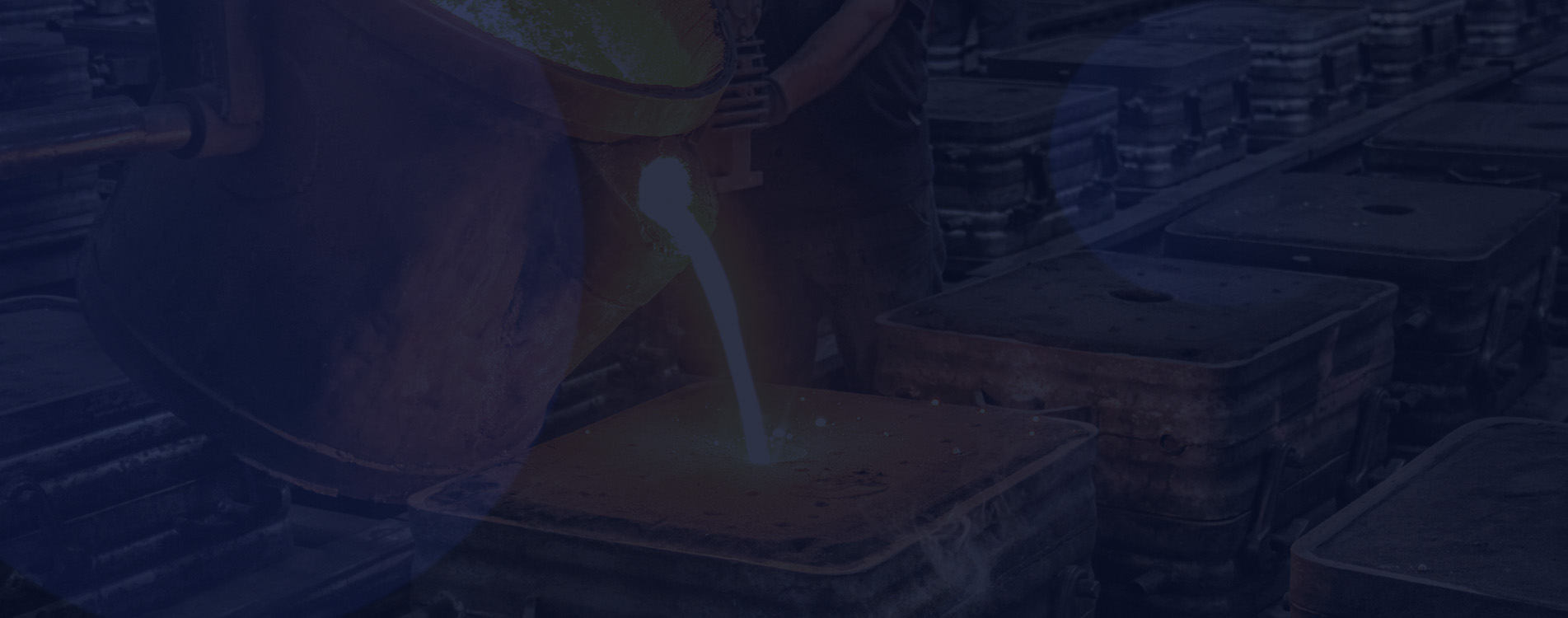
CONTACT US