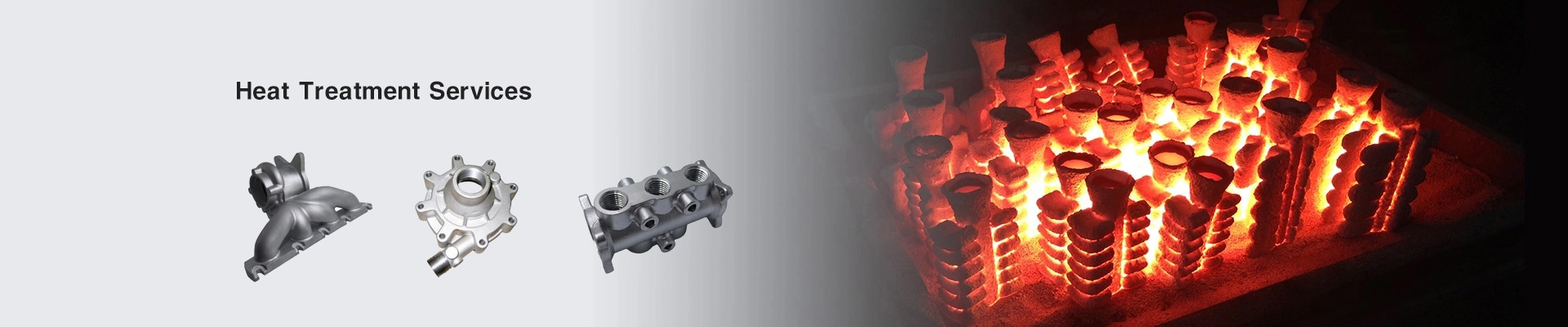
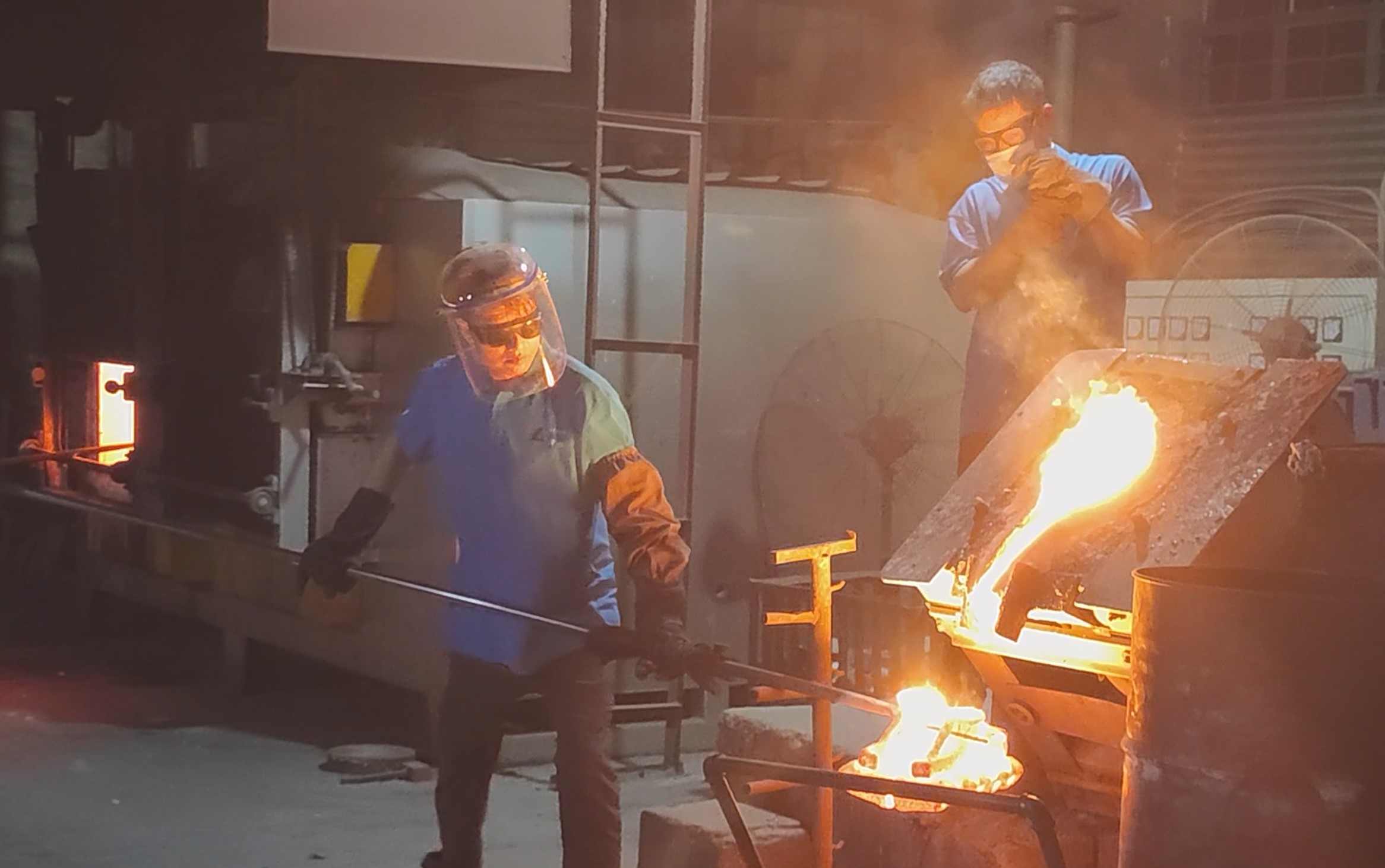
Foshan Zeren Precision Casting Company offers comprehensive heat treatment services to enhance material properties, including quenching, annealing, tempering, normalizing, aging, carburizing, and nitriding. These processes improve hardness, strength, toughness, and wear resistance, ensuring superior performance for precision-cast components. Our advanced techniques optimize microstructure and durability, meeting stringent industry standards for high-quality metal products.
Comparison Table of Heat Treatment Processes
Process | Purpose | Temperature Range | Cooling Method | Effects on Metal |
Quenching | Increase hardness and strength | 800-1000°C | Rapid (water, oil, air) | Hardens metal but increases brittleness |
Annealing | Improve ductility, relieve stress | 500-900°C | Slow (furnace) | Softens metal, improves machinability |
Tempering | Reduce brittleness, improve toughness | 150-700°C | Air cooling | Adjusts hardness and elasticity |
Normalizing | Refine grain structure, relieve stress | 800-950°C | Air cooling | Improves toughness and uniformity |
Aging | Enhance strength via precipitation hardening | 150-500°C | Air cooling | Increases strength, hardness, and stability |
Carburizing | Increase surface hardness | 850-950°C | Slow cooling | Hardens surface while maintaining core toughness |
Nitriding | Improve wear resistance and fatigue strength | 500-600°C | No quenching required | Hard surface layer with good corrosion resistance |
Quenching is a heat treatment process used to rapidly cool a metal to increase its hardness and strength. The process involves heating the material to a high temperature, followed by rapid cooling in a medium such as water, oil, or air. This process transforms the metal’s microstructure, improving its mechanical properties but also introducing some challenges like brittleness.
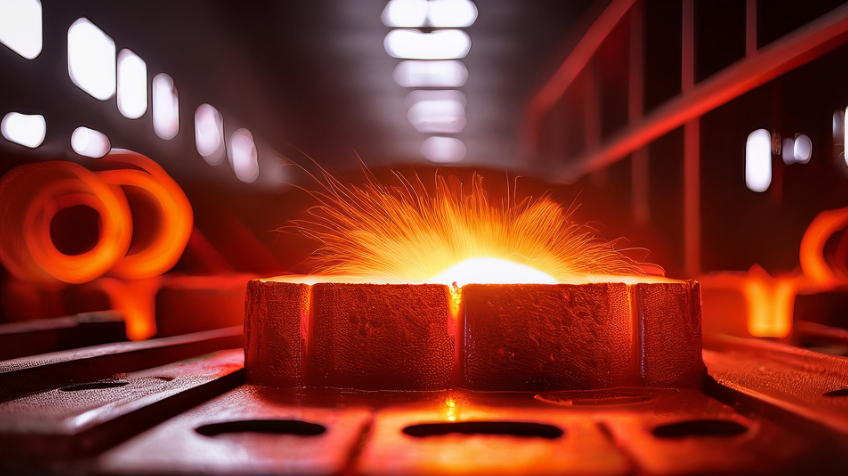
Purpose and Benefits of Quenching
Increase Hardness and Strength
Quenching rapidly cools the metal, transforming its microstructure to achieve maximum hardness and tensile strength, making it ideal for high-performance applications.
Improve Wear Resistance
The hardened surface enhances durability, reducing friction and wear, which is essential for gears, cutting tools, and bearings.
Enhance Fatigue and Impact Resistance
Quenching helps metals withstand cyclic loads and sudden impacts, improving their lifespan in demanding environments.
Optimize Mechanical Properties for Further Processing
Quenching provides a strong base that can be adjusted through tempering to balance hardness, toughness, and ductility for specific applications.
Factors Affecting Quenching
Material Type
Carbon steels and certain alloy steels are the most commonly quenched materials, though other metals like aluminum and copper alloys can also be quenched under specific conditions.
Temperature
The heating temperature determines the austenitic phase’s composition and grain structure. Higher temperatures increase the depth of hardness, but if overheated, it can lead to excessive grain growth and diminished material properties.
Quenching Medium
The choice of medium directly influences the cooling rate and the resultant hardness. Water cools the fastest, followed by oil, and air cools the slowest.
Part Size and Shape
Large or complex parts may experience uneven cooling, leading to distortion, warping, or cracking. The shape of the component can also affect the uniformity of the quench, leading to issues like residual stresses.
Modern Advances in Quenching
Vacuum Quenching
This method uses a vacuum chamber and inert gas to achieve quenching without the risks associated with conventional quenching media like oil and water. It results in cleaner parts with fewer distortions and reduced oxidation.
Controlled Quenching
Technologies like oil-quenching systems with controlled agitation, or high-pressure gas quenching, are being used to improve cooling uniformity and reduce distortion in high-performance components.
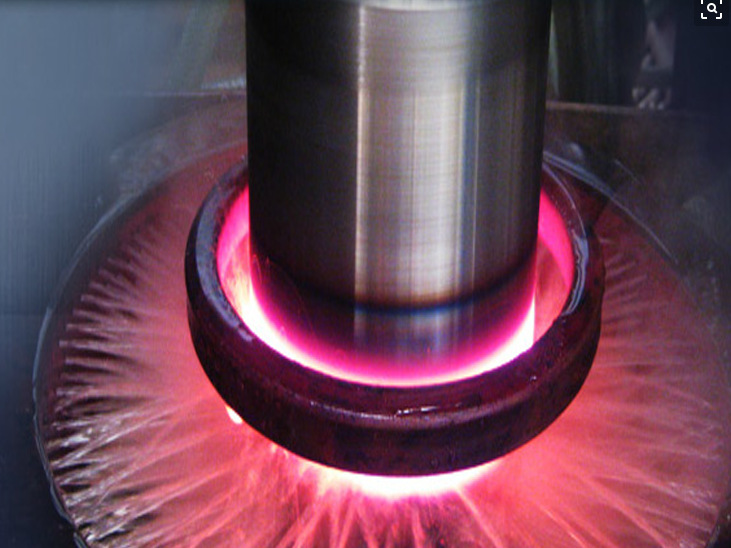
Annealing is a heat treatment process used to soften metals, improve ductility, relieve internal stresses, and enhance machinability. The process involves heating the material to a specific temperature, holding it for a period, and then slowly cooling it to achieve the desired microstructural changes.
Purpose and Benefits of Annealing
Reduce Hardness & Improve Ductility
The process softens the material, making it more malleable and easier to shape or machine.
Relieve Internal Stresses
Stresses generated during casting, welding, cold working, or rapid cooling can be removed through annealing, preventing deformation or failure.
Refine Grain Structure
Annealing helps refine the microstructure by recrystallization, eliminating defects and reducing brittleness.
Improve Machinability & Formability
Softer metals can be more easily cut, bent, or stamped, improving manufacturing efficiency.
Factors Affecting Annealing
Material Composition
Different metals require different temperatures and holding times.
Heating Rate
A gradual heating rate prevents thermal shock and uneven grain growth.
Soaking Time
Thicker materials need longer soaking times to ensure complete heat penetration.
Cooling Rate
Slow cooling prevents the reformation of hard phases like martensite.
Modern Advances in Annealing
Vacuum Annealing
Performed in a controlled environment to prevent oxidation.
Induction Annealing
Uses electromagnetic induction for localized heating, reducing processing time.
Laser Annealing
Utilized in semiconductor and microelectronics industries for precise heat treatment.
Controlled Atmosphere Annealing
Uses inert gases (like nitrogen or argon) to prevent oxidation and scaling.
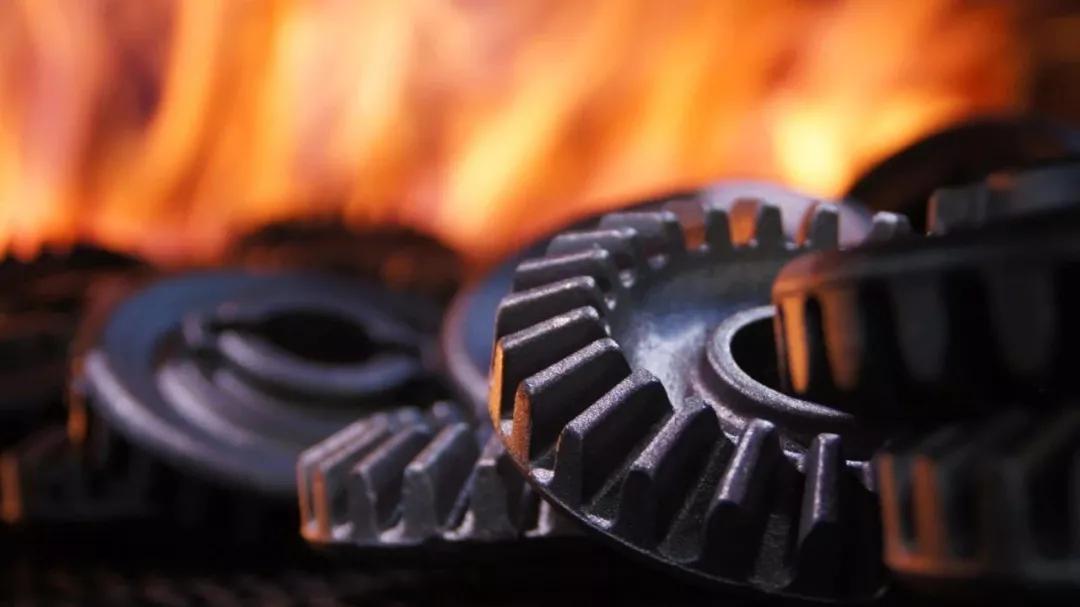
Tempering is a heat treatment process used to reduce the brittleness of quenched metals while retaining their hardness and strength. It involves heating the metal to a specific temperature below its critical point, holding it for a set time, and then cooling it in a controlled manner. This process refines the microstructure, enhances toughness, and relieves residual stresses, making the material more suitable for practical applications.
Purpose and Benefits of Tempering
Reduce Brittleness
Quenching produces a hard but brittle martensitic structure. Tempering modifies this structure, reducing brittleness while maintaining sufficient hardness.
Improve Toughness
The process increases the material’s resistance to impact and sudden loads, making it less prone to cracking.
Relieve Internal Stresses
Quenching induces internal stresses due to rapid cooling. Tempering helps redistribute these stresses, preventing warping or failure.
Optimize Hardness and Strength Balance
Adjusting the tempering temperature allows engineers to achieve the desired balance between hardness and toughness.
Factors Affecting Tempering
Tempering Temperature
Higher temperatures increase toughness but reduce hardness. Lower temperatures retain more hardness but may not fully relieve stress.
Time Duration
Longer holding times allow more complete structural transformation, enhancing ductility.
Material Composition
The response to tempering varies depending on the type of steel or alloy. High-carbon and alloy steels typically require higher temperatures.
Cooling Method
Slow cooling stabilizes the microstructure, while rapid cooling may alter phase transformations.
Modern Advances in Tempering
Vacuum Tempering
Conducted in a controlled vacuum environment to prevent oxidation and scaling.
Induction Tempering
Uses electromagnetic induction to rapidly heat and temper specific areas of a part.
Cryogenic Treatment + Tempering
Some high-performance steels undergo cryogenic treatment (-196°C) before tempering to refine the microstructure and improve wear resistance.
Tempering in Controlled Atmosphere
Using inert gases like nitrogen or argon to prevent oxidation.
Normalizing is a heat treatment process used to refine the grain structure of metals, improve mechanical properties, and relieve internal stresses. It involves heating the metal to a temperature above its critical point, holding it for a period, and then allowing it to cool in air. Normalizing enhances toughness, uniformity, and machinability, making it a widely used process in industrial applications.
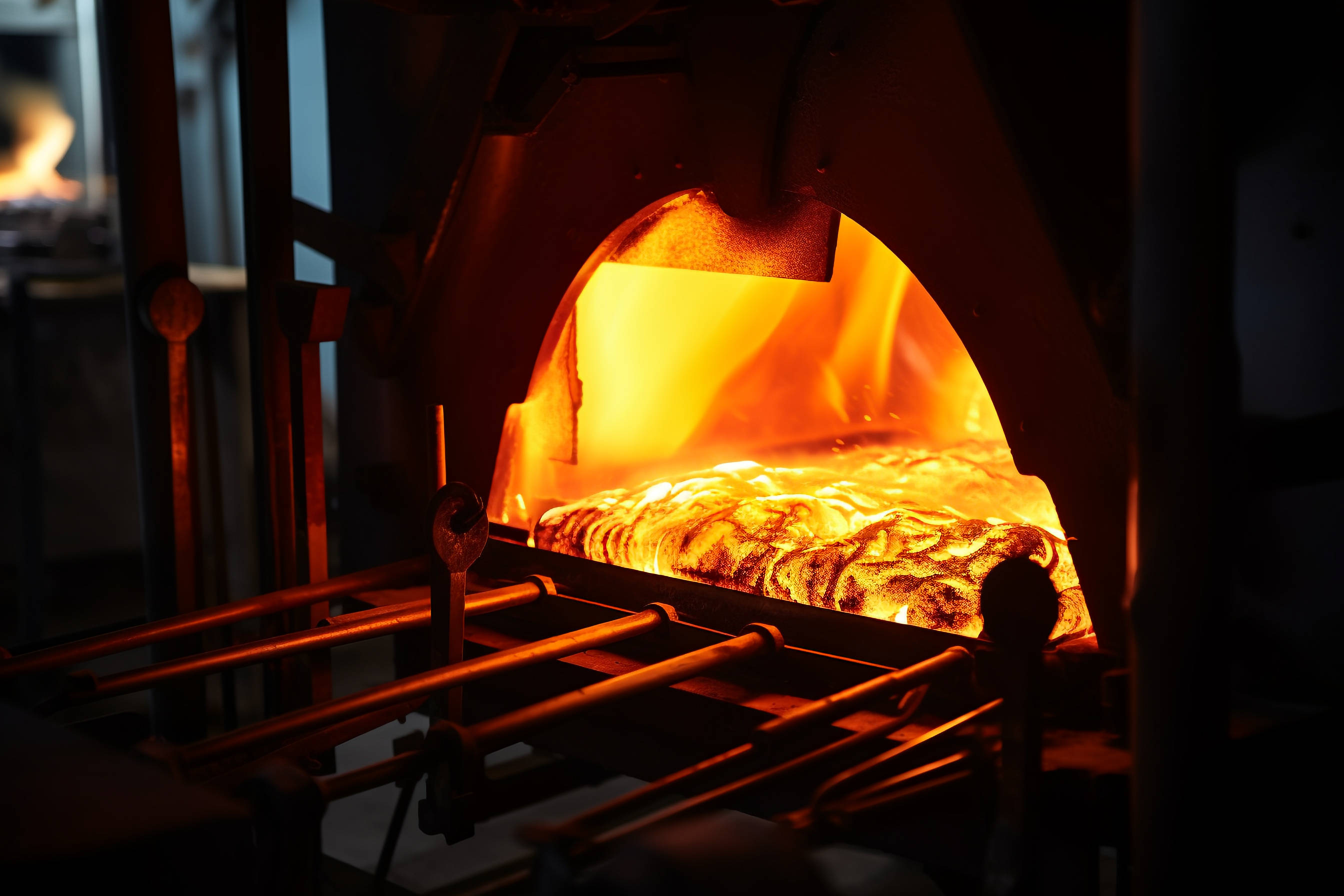
Purpose and Benefits of Normalizing
Refining Grain Structure
Normalizing helps produce a fine, uniform grain structure, which enhances strength and toughness.
Reducing Internal Stresses
It eliminates stresses caused by previous heat treatments, welding, or machining processes.
Improving Machinability
The process softens metals slightly, making them easier to cut, drill, and shape.
Enhancing Mechanical Properties
It removes structural inconsistencies such as segregation, coarse grains, and unwanted phases formed during casting or forging.
Factors Affecting Normalizing
Heating Temperature
Higher temperatures increase grain refinement but may also cause excessive grain growth if not controlled.
Holding Time
Longer soaking times allow full austenite transformation but may lead to coarser grains if excessive.
Cooling Rate
Air cooling is moderate, but factors such as air movement and material thickness affect the final properties.
Material Composition
Different steels respond differently; high-carbon and alloy steels may develop bainitic or martensitic structures.
Modern Advances in Normalizing
Controlled Atmosphere Normalizing
Uses inert gases like nitrogen or argon to prevent oxidation and decarburization.
Induction Normalizing
Rapid localized heating using electromagnetic induction for selective treatment.
Vacuum Normalizing
Performed in a vacuum furnace to eliminate oxidation and improve surface quality.
Accelerated Cooling Techniques
Some applications use fans or mist cooling to adjust the cooling rate for specific microstructural properties.
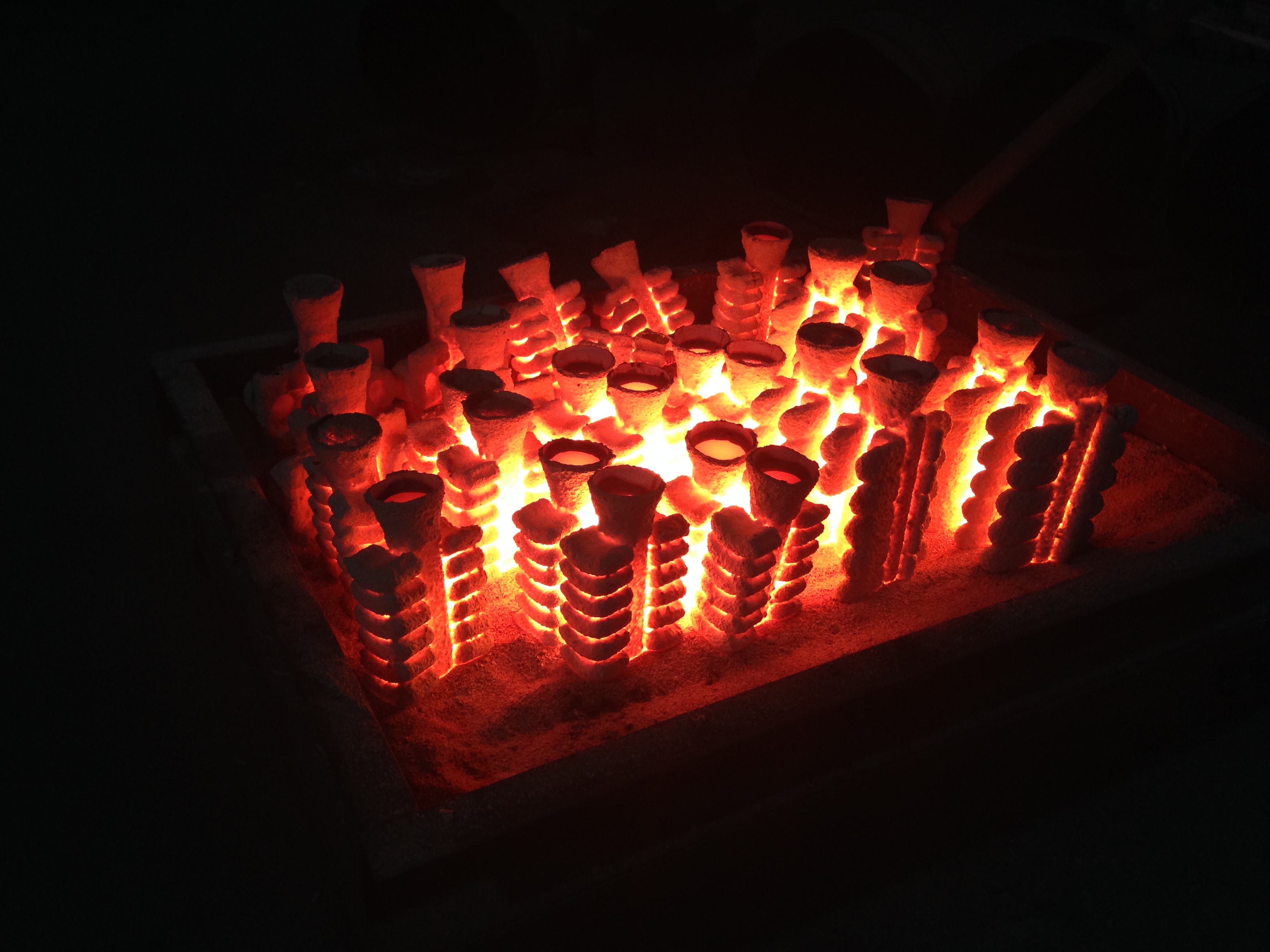
Aging is a heat treatment process used to improve the strength, hardness, and mechanical properties of certain metals and alloys by allowing the controlled precipitation of secondary phases. It is commonly applied to aluminum, copper, titanium, magnesium, and some steels. The process can occur naturally at room temperature (natural aging) or be accelerated by heating to a specific temperature (artificial aging).
Purpose and Benefits of Aging
Increase Hardness and Strength
Aging allows fine precipitates to form within the metal matrix, impeding dislocation movement and enhancing mechanical strength.
Improve Wear Resistance
The process increases surface hardness, reducing wear and friction in applications like bearings and gears.
Enhance Fatigue and Creep Resistance
Aging strengthens the material, improving its durability under cyclic loads and high temperatures.
Enhance Corrosion Resistance
In some alloys, aging can improve resistance to oxidation and environmental degradation.
Factors Affecting Aging
Alloy Composition
Different elements (e.g., Cu, Mg, Zn, Ti) form various strengthening precipitates.
Aging Temperature
Higher temperatures speed up the process but may lead to overaging.
Aging Time
Longer durations allow further precipitation but may reduce peak hardness.
Quenching Conditions
Faster quenching retains more solute atoms for aging.
Modern Advances in Aging
Cryogenic Aging
Some materials undergo deep-freezing before aging to refine grain structures and increase strength.
Microstructural Engineering
Advanced nano-precipitation control techniques optimize precipitation for superior properties.
Laser Aging
Localized heating using lasers allows for precise control over mechanical properties.
Smart Alloy Design
New alloys are developed to enhance precipitation kinetics and maximize strength.
Carburizing is a heat treatment process used to enhance the surface hardness of steel while maintaining a tough and ductile core. It involves introducing carbon into the surface layer of a low-carbon steel component by heating it in a carbon-rich environment. This process is widely used in industries requiring wear resistance, fatigue strength, and impact durability, such as automotive, aerospace, and machinery manufacturing.
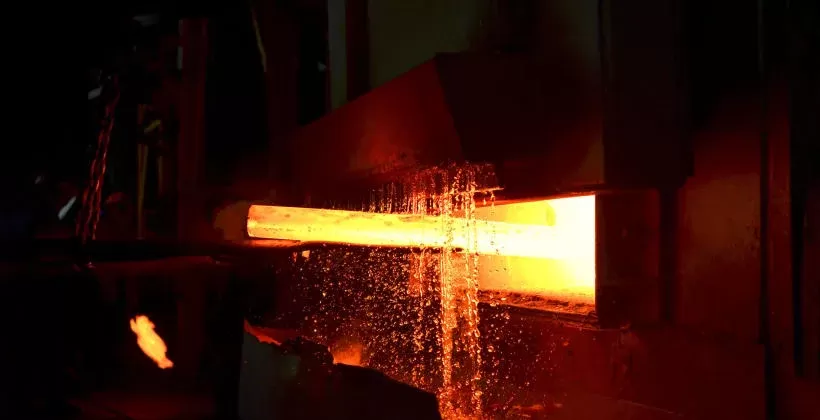
Purpose and Benefits of Carburizing
Improved Surface Hardness
Increases wear resistance, making the material suitable for high-friction environments.
Enhanced Fatigue Strength
Helps components withstand cyclic loading without failure.
Tough Core with Hard Surface
The hard outer layer resists wear, while the softer core maintains toughness, preventing brittle fractures.
Extended Service Life
Carburized components last longer due to their superior wear and fatigue resistance.
Factors Affecting Carburizing
Temperature
Higher temperatures (900-950°C) increase carbon diffusion rate but may lead to grain growth.
Time Duration
Longer times allow deeper carbon penetration but can reduce efficiency.
Carbon Source
The type of carbon (solid, gas, liquid) affects uniformity and penetration depth.
Material Composition
Low-carbon steels are most suitable, as they allow significant case hardening.
Modern Advances in Carburizing
Plasma Carburizing
Uses plasma to enhance carbon diffusion at lower temperatures with less distortion.
Low-Pressure Carburizing (LPC)
Conducted in a vacuum, ensuring better control, deeper penetration, and reduced environmental impact.
Hybrid Heat Treatments
Combining carburizing with nitriding or cryogenic treatments to further enhance wear resistance and toughness.
Nitriding is a heat treatment process used to enhance the surface hardness, wear resistance, and fatigue strength of steel and other alloys by diffusing nitrogen into the material's surface. Unlike carburizing, nitriding occurs at relatively lower temperatures (500-600°C) and does not require quenching, reducing distortion risks. It is widely used in industries requiring high wear resistance, corrosion protection, and enhanced fatigue strength, such as aerospace, automotive, and tooling.
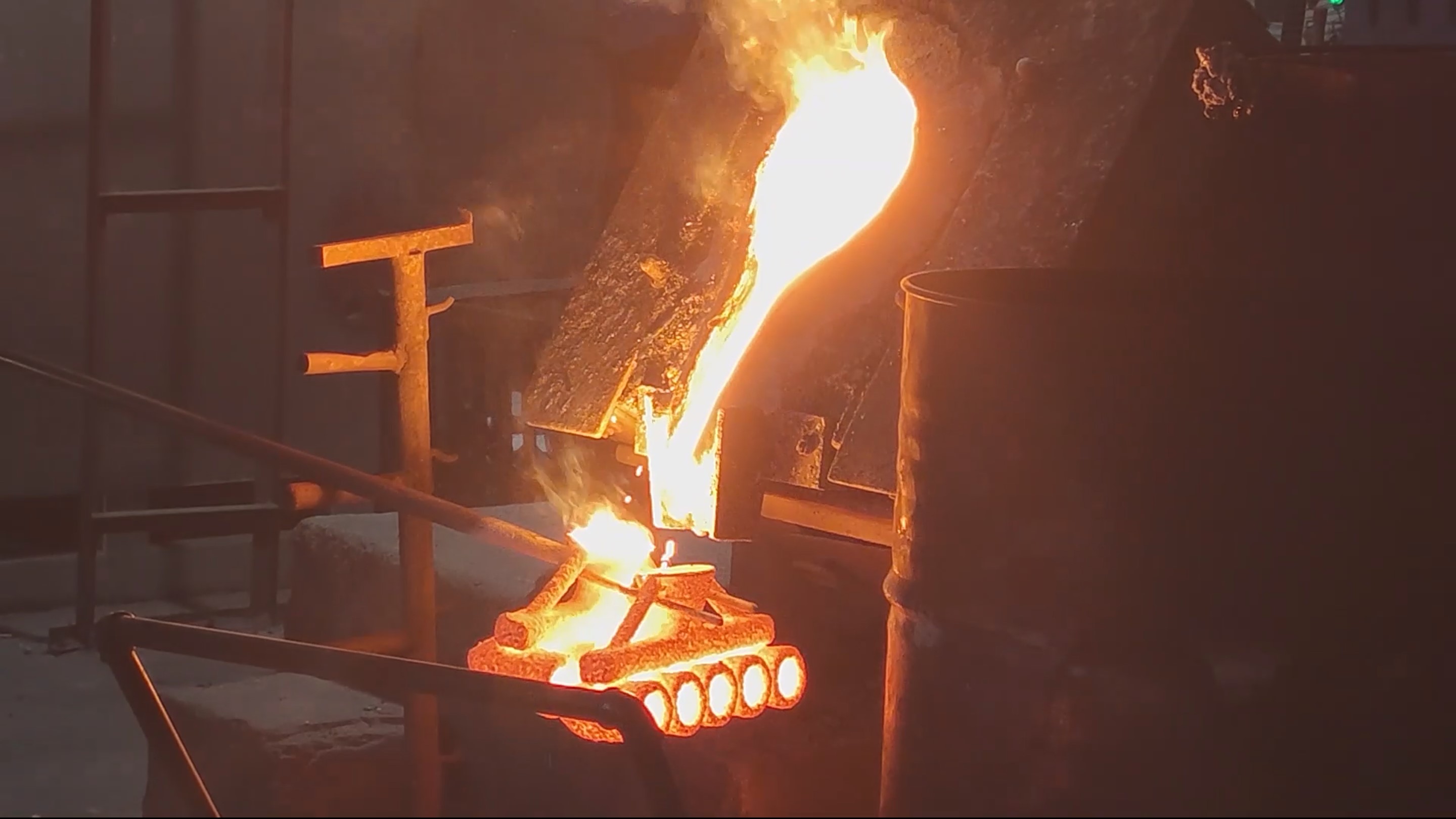
Purpose and Benefits of Nitriding
Increased Surface Hardness
Produces a hard, wear-resistant nitrided layer (up to 1000-1200 HV).
Improved Wear Resistance
The hard surface layer resists abrasion and extends component life.
Enhanced Fatigue Strength
Nitriding introduces compressive surface stresses that help prevent crack formation under cyclic loading.
Minimal Distortion
Since nitriding occurs at lower temperatures without quenching, it minimizes the risk of warping or cracking.
Factors Affecting Nitriding
Alloy Composition
Steels containing Cr, Mo, Al, V, Ti form stable nitrides, improving nitriding efficiency. Common nitridable steels include 4140, 4340, H13, and stainless steels.
Processing Time
Longer treatment leads to deeper case depth, but too much nitrogen can cause embrittlement.
Temperature Control
Higher temperatures accelerate diffusion but may reduce surface hardness.
Gas Flow Rate and Pressure
In gas and plasma nitriding, precise control of nitrogen flow and pressure is crucial for uniformity.
Modern Advances in Nitriding
Nano-Structured Nitriding
Enhances surface properties by optimizing nitrogen diffusion at the atomic level.
Hybrid Nitriding + Carburizing (Carbonitriding)
Combines carbon and nitrogen diffusion for deeper hardening layers.
Controlled Atmosphere Nitriding
Uses optimized gas mixtures to precisely control case depth and hardness.
Low-Pressure Plasma Nitriding
Reduces environmental impact and provides better control over nitride formation.
With advanced technology and years of expertise, Foshan Zeren Precision Casting Co., Ltd. delivers customized surface treatment solutions tailored to diverse industrial needs. Whether you require enhanced wear resistance, corrosion protection, or a refined finish, our precision-driven processes guarantee superior results. Trust us to provide cost-effective, durable, and aesthetically optimized metal finishing solutions for your business.
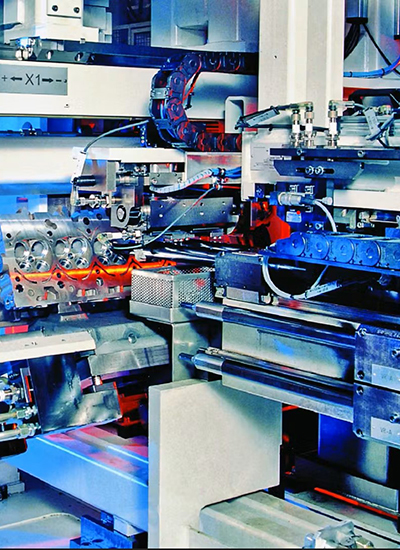
Agriculture
Machinery
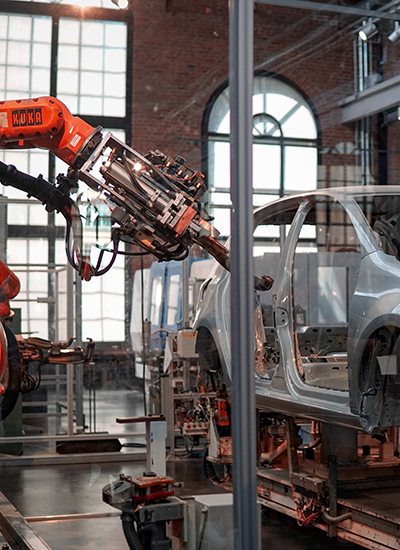
Automotive
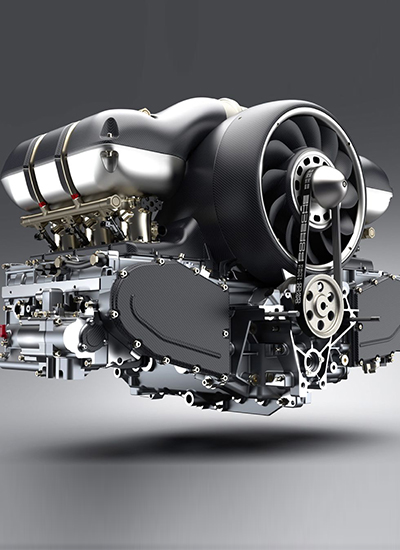
Energy
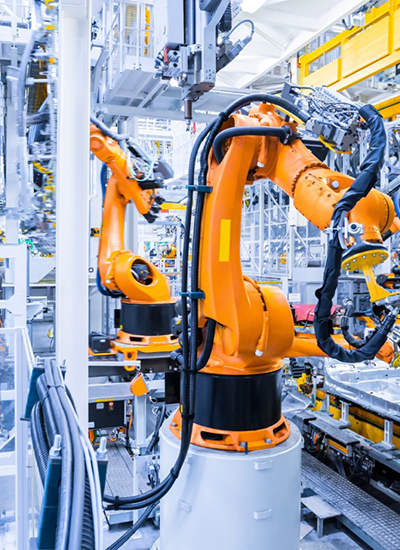
Industrial
Machinery
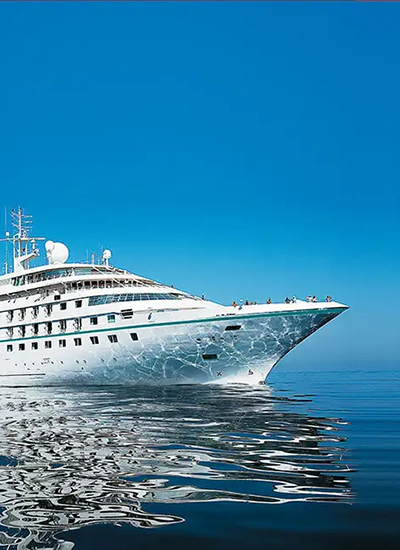
Marine
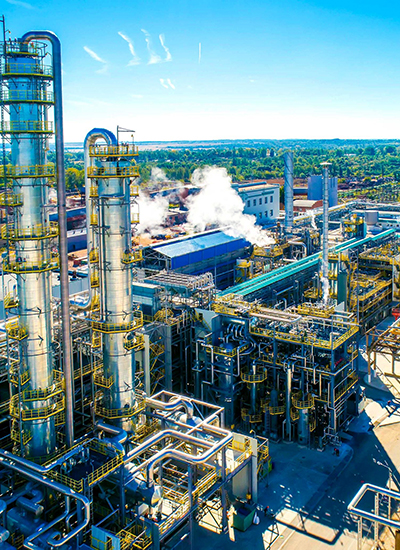
Petrochemical
Machinery
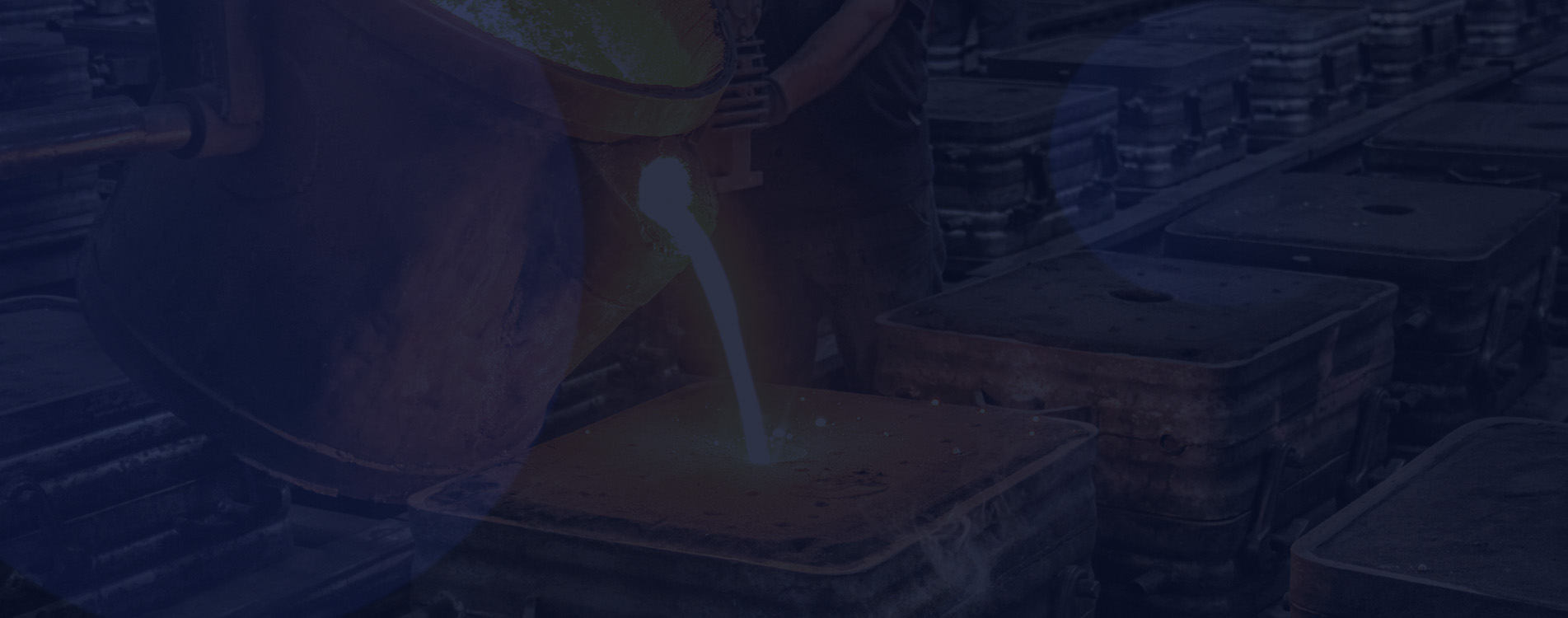
CONTACT US